第10回:搬送を考慮したレイアウト設計 ~設備の配置を決めよう!搬送を考慮した設備位置の決定~
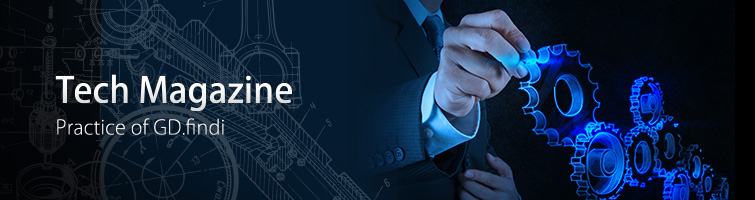
設備の配置を決めること、すなわち設備レイアウト設計は、通路や設備のサイズなど様々な要因を考慮して行われなければなりません。
考慮すべき点の 1 つに、「搬送」による生産性への影響があります。
今回はこの搬送に着目して、生産性への影響を見て設備の位置を決定する方法をご紹介します。
仮定する生産モデルは以下となります。
工程 : 搬入[20 秒](搬入口) → 加工[30 秒](加工機) → 搬出[15秒](搬出口)
※ かっこ内は使用する場所や設備
距離 : 搬入口と搬出口の距離は 45m 、加工機の大きさは幅・奥行ともに 5m
搬送 1 : 搬入口 → 加工機(部品 1 個ずつ)、搬送 2 : 加工機 → 搬出口(部品 5 個ずつ)
搬送 1 と搬送 2 はそれぞれ担当された作業者が搬送を行うものとします。
しかし、搬送 2 を担当する作業者は加工機での加工の作業も担当するものとします。
さて、ここで搬送方式(搬送する部品数)と搬入口・搬出口が前提として変更できない場合、加工機はどこに配置するのが良いでしょうか。 特に制約が無い場合、搬入口と搬出口を結んだ直線上に加工機の搬送場所が来るように、加工機を配置すればよいというのは明らかですが、直線上のどこに配置すればよいでしょうか。
1 搬送回数を考慮した配置のモデル作成
1 個ずつ搬送する搬送 1 を行う回数は、搬送 2 のそれよりも多いのは明らかです。
まずは、搬送 1 の距離が短くなるように配置してみましょう。
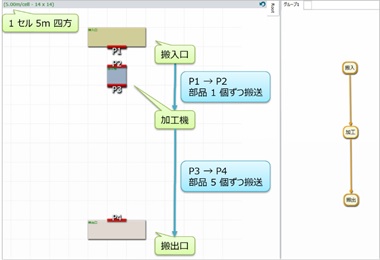
フロアプランの設定から、セルサイズを 5m にし、各設備および各工程を定義します。
さらに、各設備に搬送点を作成し、搬送点の間に搬送アクティビティを定義します。
搬送アクティビティでは、 P1 → P2 の搬送を作業者 1 が、 P3 → P4 の搬送を作業者 2 がそれぞれ行うよう設定します。
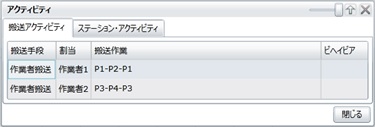
また、作業者 2 に加工作業を担当させるよう設定します。
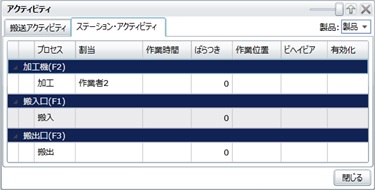
これでレンダリングを実行してみます。
ここでは、製品の生産目標数を 100 個、投入ロット数を 10 個ずつとします。
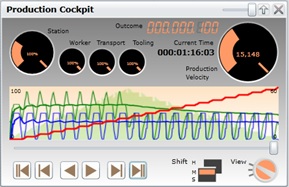
結果は、上記のように 1:16:03 で目標数に達することが分かりました。
では、この設備レイアウトが最も生産性の高いものでしょうか。
アニメーションを見ると、そうではないことが分かります。
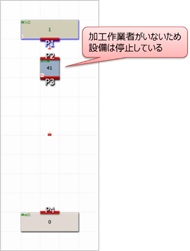
実は、加工機は、加工を行うために必要な作業者が搬送のために不在となっており、停止してしまっています。
これがネックとなり、生産性に影響が出ていることが予測されます。
2 加工作業者を考慮したレイアウトへの変更
では、加工作業を担当する作業者 2 の搬送が、最も短くなるようにレイアウトを変更してみましょう。
変更された加工機の配置は以下となります。
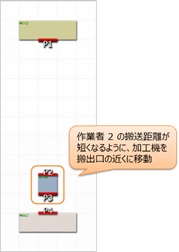
この状態でレンダリングを実行し、結果を見てみます。
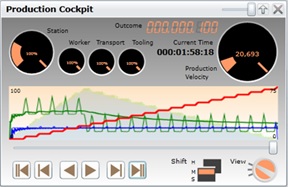
今度は先ほどのケースと比較して生産性が落ちてしまいました。
これは搬送 2 の距離を短くしすぎたため、 1. で考慮した「搬送回数が多い搬送距離」という要因が生産性に影響を及ぼしてしまった結果です。
3 生産性の高いレイアウトへの修正
では、加工機はどの位置に配置されるのが最も生産の高いレイアウトなのでしょうか。
上記 1. と 2. をともに考慮に入れ、加工機の位置を変えながらシミュレーション結果を比較し、製品の生産目標数を達成する時間が最も短いケースを選択します。
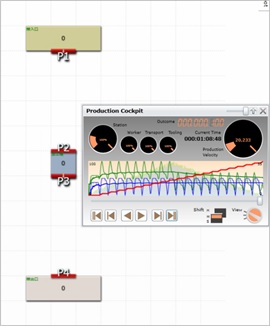
何度か加工機の位置を変えてシミュレーションを行ったところ、最適な位置は搬入口と搬出口の間のちょうど中間点(搬入口から 20m 地点に加工機への搬入が行われる場所)ということが分かりました。
このようにして、レイアウト設計時に搬送を考慮したシミュレーションを繰り返すことで、最適と判断できる設備の位置を決定することができます。 是非、ご活用ください。分かります。
なお、GD.findi に関する詳細は下記ページよりご覧ください。