第1回 進化せよ!日本の「モノづくり力」

関ものづくり研究所/関伸一氏 × レクサー・リサーチ/中村昌弘
新対談シリーズ第1回目のゲストとして、関ものづくり研究所(http://www.sekimonodzukuri.jp/)の関伸一代表にお越しいただいた。28年にわたるモノづくり企業での勤務経験を持つ関さんは、ローランド ディー.ジー勤務時代の2000年に、1人完結のデジタルセル生産システムである「デジタル屋台(DShop)」を構築し注目を浴びた。2010年に同研究所を設立後、最新のデジタルモノづくり技術を活用し、生産現場の品質向上や生産性向上に向けた改善活動をサポートしている。最近では連載コラム「関伸一の強い工場探訪記」(「日経ものづくり」)を始めとする執筆活動や講演、大学での講義などに精力的に取り組んでいるほか、日経BP社主催「日本の強い工場アワード」審査員も務めている。
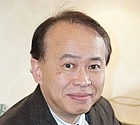
「自社の強み」を知る企業が生き残る
中村 今日は「プロフェッショナルの知とデジタルエンジニアリング」対談シリーズの第1回目として、関モノづくり研究所の関 伸一さんにお越しいただきました。関さん、こんにちは、今日はよろしくお願いします。
さて、早速ですが、関さんが日ごろの活動を通じてモノづくり現場を数多くご覧になってきた中で、いろいろとお考えのことがあると思います。まず、そこからお話を聞かせていただけますか。
関 非常にポジティブにアプローチしている企業と、取りあえず仕事が来るからということで、現状維持に落ち着いている企業との二極化が進んでいますね。頑張っている会社は非常に積極的で、たとえば「日経ものづくり」2013年6月から7回にわたって連載した「関伸一の現場探訪記」の中で、浜松市にある中堅工作機械メーカのエンシュウを取材しました。同社では、本社工場(高塚工場)で汎用マシニングセンタを製造する一方、浜北工場では工作機械の製作で培ってきた〝エンジン〟を活かしてトランスファーラインを作っています。オーダーメードで工場設備を作り、中国など海外の企業に売っているのです。そのように、設備を売るというビジネスの流れが1つあると思います。
中村 そうですか。
関 それから最近、規模が小さな企業にも3次元CADが導入され始めています。これも導入する気がまったくない企業と、経営者みずから「取りあえず買ってみよう」という動きのある企業と、完全に二極化が進んでいますね。じつは、2008年に起きたリーマン・ショック後に、日本における3次元CADの導入数が大きく伸びているのです。
中村 伸びているんですか。
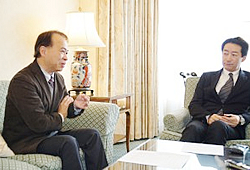
関 そうなんです。わかっている経営者は「こんな不景気がいつまでも続くわけがない。将来、景気が上向いた時に備えて3D武装をしよう」と考え、3次元CADを導入しました。長年にわたる不景気で疲弊し、廃業はほぼ避けられないだろうという工場も見ていますが、モノづくりを真剣に考えて小さな会社が3次元CADを買うというアプローチから、「これからはモノだけでなく生産設備を売っていく」という企業まで、動きとしては非常に面白いと感じています。
中村 (モノだけでなく)システムとしての販売と、デジタルエンジニアリングシステムの導入が、モノづくりにおける新しい動きとして現れてきているのですね。ですが、中堅企業などで新しい潮流を追っているところは限られますし、大手企業も製造現場、生産技術を始めとする中間部門、経営部門を含めて、そういう動きにはなっていません。いろいろと悩み、模索しながらも、何も変わっていないのが現状です。
関 そうですね。私は2つ問題があると思います。まずは事業承継、すなわち「代替わり」。私の地元である浜松地域では、経営者が7、80代になっても社長をやっ
ているケースが多いのです。私は血縁で会社を承継するなら、子供が3、40代で継がせるべきだと思います。
中村 おっしゃる通りです。
関 もう1つ、これから中小企業がやるべきことは企業間連携なのですが、そこで問題になるのが、中小企業が自社の強みをわかっていないこと。外から見て「その技術はすごい」というものがあるのに、それを理解していないから売り込みができない。
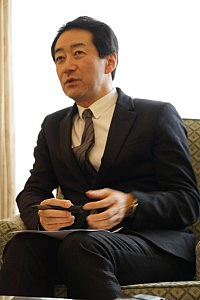
中村 関さんがおっしゃる第1点目の事業承継は、中小企業の経営課題。第2点目については、産業構造の問題から来
ていると思います。日本には自動車業界を始めとして、大手セットメーカの下にTier1(1次請け)、Tier2、Tier3といったサプライヤがひしめく産業構造があり、ある意味、安定的かつ質の高い受注が確保される中で、各社の技術力や現場力が育ってきました。ところがそれは、自社の強みを知らなくても、モノづくりができていたということでもあるわけです。自社の強みに対する認識が持てないというのは、仕事の相手先が固定されていて、かつ指導もしてもらえるというサプライチェーン構造の中で生じた現象です。
関 そうですね。
中村 その意味で、自社の強みを知ることは、中小企業が従来のサプライチェーン構造の外にある新しい取引形態に進
んでいくための学びとなり、力をつけていくための源泉になるでしょう。そこで、日本に根強く残るこうしたサプライチェーン構造をどう打破していくかが問題になります。ところが中小企業にとってBtoBビジネスや、新しい案件を獲得していくことは難しい。そもそも自社の力を理解できていないので、それを新しい分野にどう適用していけばいいのかがわかりません。
関 浜松に国本工業という元気な会社があるんです。同社はパイプの曲げ加工が得意で、かつてはヤマハ発動機にオー
トバイのスタンドを100%納入していました。ところがヤマハ発動機が海外に出るようになり、最終的には95%の仕事がなくなりました。でも国本工業は自社の強みをよく理解していて、鋳物製の部品をパイプ加工で置き換えた試作品を持ってトヨタ自動車に売り込みに行ったのです。その結果、当時従業員30人程度にすぎなかった同社が、Tier1になりました。
中村 自動車業界の産業構造で見ていくと、仮にTier1を取れたとしても、一次サプライヤであって、自社製品を扱っているのではないわけですね。日本のモノづくりの産業構造は特殊です。アメリカでは中堅企業でも自社製品を持っていることが多く、中堅企業が大企業のサプライチェーン構造の中にあまり入っていません。アメリカでは今モノづくりの国内回帰を進めていますが、おそらくそういう地盤がベースにあるのでしょう。
関 そうですね。
中村 日本の場合、企業がどこかのサプライチェーンに入っていくという構造なので、そこを打破することが、日本のモノづくりの復権におけるポイントになると思います。トヨタを攻めるのもいいですが、大変なことではあっても自社製品を作るとか、海外市場をどう開拓していくのかということも考えていかないと。
関 最初に務めた会社がまさしくTier1でした。私がそこを飛び出したのは、自社ブランドを持っていなかったからです。「自社ブランドで製品を作ろう」と3年間社長に直訴し続けたのですが、実現しませんでした。
中村 他人に言われて作る、いいものを作る、それも大切です。でも品質やメンテナンス上、経営上の責任が伴うにしても、自分で考えてモノづくりをすることで、仕事が面白くなるだけでなく、企業の個々の活動がより価値のあるものになります。
関 エンジニアにとって、自社ブランドの存在は大きいですよね。自動車部品にしても、設計から製造までサプライヤがほとんどの仕事をしているのに、社名が表に出てきません。それではエンジニアは最上位の達成感を得ることはできないでしょう。
中村 昔は大手電機メーカでなければできなかった製品が、新興メーカでも作れるようになってきています。これまで大手企業のサプライチェーンの中で製造していたものを、自社製品として作ることが可能になっているケースもある。資金面や市場開拓などの問題もありますが、時代がそのように動いている以上、海外の新興企業に市場を取られるのではなく、日本のモノづくりを活かした自社製品開発の動きがあってもいいのではないでしょうか。
1 / 2