第4回 「価値づくりの突破口はモノづくりにこそある

「主観的な価値は汎用化する」
中村 延岡さんはご著書で「組織能力のマネジメントは難しい」と述べていますが、その通りだと思います。日本のモノづくり企業はこれからどうしていけばいいのでしょうか。組織能力のマネジメントという方法論なのか、それとも人の意識の問題なのか…。
延岡 最終的には企業のトップや上層部が(組織能力のマネジメントを)理解しないと駄目なのですが、その前に何が必要かと言えば、ミドルマネージャが小さな成功体験を積み重ねていくことしかないと思います。
中村 そうですね。これまで日本のモノづくりはミドルが支えてきた部分が大きいと思うのですが、そのミドルの役割や力が劇的に低下していることが大きな問題です。成果主義の影響も大きいと思うのですが、現場力、現場力とは言っても、ミドルが何も見ないまま、結局、現場に丸投げをしている状態です。
延岡 だから最初の話に戻るのですが、日本の製造業の中でモノづくりの地位が低下し、短絡的に「製造よりも商品開
発、商品企画だ。モノづくりは昔ほど重要ではない」ということになってしまっています。そうなるとミドルマネジメントの力量もモチベーションも失われてしまいますし、実際に人も減っています。
中村 そうですね。
延岡 それでも日本企業はいろいろな意味で、モノづくり現場がうまくやれ
ば強いのですから、本当に価値づくりを行っていくなら、モノづくりとは元来、価値を創るためのものであり、そのために現場やミドルマネジメントの力やモチベーションをいかに高めていくかが死活問題であることを再認識すべきです。にもかかわらず、先ほどから話しているように、日本企業はアップルのiPhoneについて「筐体だけに3000円のコストをかけることがはたして妥当か」と思考停止している状態で、なかなかトップが「モノづくりでこそ価値を創っていくのだ」という認識を持てません。ですから、たとえ小さなことでも、現場の課長クラスを始めとするミドルマネジメントが「モノの作り方だけでこれだけ商品力が向上した」という成功体験を積み重ねていくことが非常に大事です。
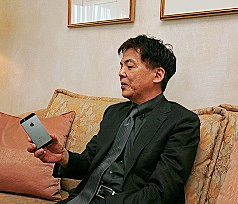
中村 延岡さんが『価値づくり経営の論理』に書かれているように「モノづくりを徹底しても、価値づくりに結びつかないのであれば、モノづくりに関して力を抜いた方がよいと考える企業が見られる」というのは問題ですね。
延岡 商品開発において機能やスペックを追っても過当競争になり、どれだけあがいても勝ち残るのは難しいということを、誰もがわかっているはずです。モノづくりの部分は、商品のように簡単にはテアダウン(比較対象の商品を分解調査すること。リバースエンジニアリング)できません。外からは見えないところでやっていますから、モノづくりを価値づくり活かすことがきちんとできれば、商品スペックほど簡単には真似されず、本当の強みになっていくはずなのです。日本企業は、モノづくりの地位の低下にどこかで早くストップをかけて、「モノづくりこそが商品の価値を生み出す」という文化を取り戻す必要があります。
中村 実際、「モノづくりは重要ではない」、むしろ「モノづくりでやっていても勝てないから外部に投げてしまおう」、「ODM(相手先ブランドによる設計製造)でやってしまおう」という風潮がかなりあるのを感じますね。
延岡 いまだに日本企業は、海外生産やアウトソーシング、ODMでいくべきか、自社で内製すべきかという二極分化の状態です。ところがキーエンスのように本当に成功している企業は、ファブレスとは言いながらも、生産技術はすべて自社がきちんとおさえています。アップルも年間1兆円近い設備投資を行っていますが、ファナックのロボットを自社で大量に購入し、FOXCONNなどのEMSメーカに「この通りに使いなさい」と指示して、付加価値の低い部分の作業だけを任せている。アウトソーシングを行うにしても、本当に大事な部分は自分たちがコントロールするのが正解だと思います。
中村 そうですね。
延岡 ところが、「どうせ外に出すなら、手離れが良くなければもったいない」と考える日本企業がいまだに多いようですが、そうなると日本の強みがまったく活かされません。その一方で、すべてを自社で作るのがいいかと言うと、それも疑問です。たとえば付加価値を生んでいない手作業の部分を、外部に委託することは悪くないでしょう。
中村 手前味噌になりますが、そこに縦串、横串をいかに刺すかが勝負だと思います。ODMにしても内製にしても、基本的には現場のことが本当にわかっているのかが問われる一方、QCDの話にもつながるかもしれませんが、モノを作るための生産システムをしっかりと運営していくための方法論を確立しなければなりません。その1つの手法がエンジニアリングチェーン・マネジメント(ECM)であり、それが、われわれのできることだと思っています。場合によっては今後IoT(モノのインターネット)を活用し、(生産シミュレータなどのツールに)さまざまな機器のテータを取り入れていくことになるかもしれません。生産シミュレーション等を活用し、「この製品はこのように作れば成功を担保できます」というモデルを、国内および海外の製造拠点、場合によってはODM先に構築し、実行部分もマネジメントできる仕組みがあれば、自社でも国外でもODMでも同じ環境が実現可能です。それができることで初めて、1本筋が通ると思いますね。
延岡 なるほど。
中村 今まではそこを人が手がけてきたのです。ところが海外の子会社でも、日本から製技の担当者が現場に行って立
ち上げを行い、仕事が済んで帰ってきたらそこでおしまい。そうではなくて、何らかの形で現場と常につながる仕組みを構築する必要があります。
延岡 そこをつなげてマネジメントをする際、1つ注文があるとすれば、(商品づくり)全体における自分たちの仕事の価値がわかる仕組みが必要だということです。差別化できる価値を創ろうと思うと、どこかに自社の工場でしかできないような(技術的・ノウハウ的に)難しい部分が要るからです。ECMで商品企画から生産準備の段階までを全部シミュレーションできるなら、「(この部分の)コストはこれだけ高くなっても、こうすればこれだけの価値が生まれる」とか、あるいは「こういうやり方をしたらどうなるのか」という、戦略の違いもある程度評価することができるようになるわけです。(この一連の対談の中に「3D一気通貫モノづくり」の話題も出ていますが)、価値づくりも合わせた一気通貫のマネジメントが必要ですね。
中村 そうですね。
延岡 すべてが簡単になるところから価値は生まれません。だからどこかで、難しくはあっても、本当に価値を生む部分を作らなければいけないのです。そういうものを商品づくりに取り込んでいくことで、全体としてどういうシステムやモデルになっていくのかというところまでをきちんと評価できるといいですね。
中村 主観的な価値、すなわち意味的価値を含めてですよね。客観的な価値の部分で言うと、原価方式のようなことはやれるのですが、それでは差別化になりません。自社の固有技術がもたらす意味的価値を、何らかの形でモデリングして価値づくりに載せる仕組みが必要です。当社では、生産シミュレーション技術を活用することにより、「あるべき生産モデル」を作り込む「SIM(Simulation Integrated Manufacturing)」を提唱していますが、製品のエンジニアリングチェーンの中で、「これとこれが、意味的価値において圧倒的に差別化要素になるから必ず入れる」、というモデリングができたらいいですね。
延岡 「価値の強さ」と、他の企業ではなかなかできないという「難しさ」がポイントですね。今日は最初に述べた価値づくりの話にどうしても戻ってしまうのですが、産業革命後に大量生産が始まった頃に、手作りの本当の良さといった価値が失われてしまったということは、デザインの世界でもよく言われていることで、そこをうまく取り入れていくことが価値づくりの1つのポイントです。アップルが削り出しという、いわば原始的なモノの作り方を取り入れたのも似たような話で、吉田カバンも全国約80人の職人や工房と連携し、すべてメイド・イン・ジャパンで製品を作っています。今どきカバンをすべて国内で作るというのはとても考えられないことですが、同社は高いスキルやノウハウを持つ職人が手作りでカバンを作ることに高い価値を実現し、手作りというものをうまくネットワーク化して、あれだけの量のカバンをメイド・イン・ジャパンで作っています。ある意味でアップルの例に似ていると思うのですが、商品づくりにかなり難しいことを無理やり入れ込むからこそ、逆にデジタル的なネットワークの管理をきちんとやれば、手作りの要素をいろいろなところに入れ込みながらも、全体的にはうまくマネジメントができて、良い商品を作ることができるのです。
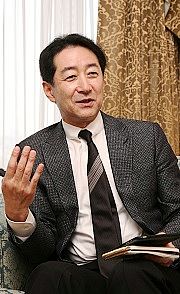
中村 そうですね。
延岡 そういう価値が非常に高い部分は、コストがかかったり、ある意味で無駄に近いとも言えますが、ツールをうまく活用することで、全体を効率よくマネジメントできます。(技術的・ノウハウ的に)難しいことから意味的価値が生まれ、それが商品づくりに取り入れられることが、日本の目指すところだと思います。
中村 それによって新たな価値が生まれ、強い差別化ができるわけですね。
延岡 「インダストリー4.0」も、少し賢い人が考えれば、社内だけなら比較的簡単です。吉田カバンのように、社外も含めたネットワークをうまくマネジメントするということになると、大きな力を発揮する可能性がありますね。
中村 ある意味、社内であれば日本でも、標準化はしていないものの、個別的には「インダストリー4.0」に近いことをすでに手がけているわけです。「インダストリー4.0」では、各設備がインテリジェントな機能を持ち、互いに通信しながら「スマートマシン」として自律的な動作で連携します。私は、そういう「スマートファクトリー」の中で連携するのは設備だけである必要はなく、人も「スマートマン」として連携すべきだと思います。
延岡 なるほど。
中村 今われわれが手がけているのは、簡単に言えば「インダストリー4.0」の「人間版」で、作業者にスマートフォンを持たせてさまざまな指示を出し、作業者もその結果のデータをスマートフォンで入力しフィードバックするというものです。それが職人芸なのか単純作業なのかはさておき、人の力や人の作業がスマートマシンとともに連携していくという新しい形態があり得ると思います。20世紀における大量生産システムの先駆けとなったテイラーの科学的管理法(テイラー・システム)は、当時としては新しいコンセプトでしたが、モノづくりはそこでいわゆる「手続き型」に変化しました。今ではそれがモノづくりの上流の端にまで広がり、その揺り戻しが起きているのでしょう。下流の方はまだですが、ある意味で、テイラー以来の「手続き型」のモノづくりが終焉に近づいていると考えられます。だとすれば、「動的型」という言い方が適当かどうかはわかりませんが、従来とは異なる仕事の進め方を構築することが不可欠です。「動的型」のモノづくりの中で、意味的価値を生み出すコア技術を作り込んで差別化を図り、もちろん従来通りQCDにも励んでいくという、その道を進んで行かなければならないということですね。
延岡 「手続き型」のモノづくりの効率がいいのは間違いありません。ただ、それが低次元の「手続き」で終わってしまうなら、非合理的なルールに縛られた官僚組織と同じです。ですからここで、価値そのものの向上を図り、より高い次元での「手続き」をなるべく早く構築しなければなりません。中村さんはその「動的型」のモノづくりと、より高い次元の「手続き型」のモノづくりの両方をやられないと…。低い次元の「手続き」の話だけをしても仕方がないですからね。
中村 「価値モデル」という言葉が適当かどうかわかりませんか、価値そのものを何らかの形で評価できたらいいと思いますね。
延岡 そうですね。しかも(価値づくりの)ネタになるものは、センスのある人がきちんと考えれば、設計開発よりモノづくりの方が、ずっと多いのです。たとえば半導体はそのほとんどが標準品ですから、商品開発の段階でどう差別化し、自社だけにしかできない価値を生み出すのかを考えること自体が難しい。その一方で、製造の話になると、材料だけでも何百種類あり、アップルもアルミ材だけで何種類も使っています。作り方もいくらでもありますし、「触って気持ちいい」というユーザインターフェイスの部分でも、かなり製造が重要です。まさに、真似をされない価値を生み出すポイントになるのが製造であり、そこを本当にきちんとやっていくことが重要だと思います。
中村 DFM(Design for Manufacturing/製造を考慮した設計)やDFA(Design for Assembly/組立性を考慮した設計)などの評価モデルに即しているかどうかわかりませんが、たとえばそういうモデルの中で「意味的価値」を記述することができるのか、という難しい問題もあります。
延岡 かなり難しいですね。しかし価値を生み出すことにおいては、やはり人が大事です。日本にはそこを担う力を持った人材が十分にいますからね。
中村 本来は、そういう人材がいるのですよね。
延岡 いるんです。じつは私は今、マツダのデザインの研究をしています。皆さんがこの考え方に同意して下さるかどうかわかりませんが、私はマツダのデザインが日本では圧倒的にトップを走っていると思っています。その1つのポイントは、デザイナが描いたイメージをクレイ(粘土)で造形するクレイ・モデラーに、アーティスティックな能力が非常に高い人を使っていることにあります。
中村 そうなんですか。
延岡 デザイナに、デザインの良さを表現させようというのが普通の会社です。ところが本当に美しい曲面をデザインしようと思うと、彫刻の芸術作品と同様に、コンマ数ミリという微妙な削り具合でカーブを作る作業が、まさに顧客価値に直結するのです。その意味で、モノづくりで本当に高いスキルを持った人が、そういう部分を顧客価値に結びつけることを可能にするようなマネジメントが大切です。普通の自動車メーカではデザイナがスケッチを描き、それをもとにしてクレイ・モデルを作るというオペレーションだけを、クレイ・モデラーにやらせています。要は単なるオペレータなのですが、マツダでは、クレイ・モデラーの中の数人が、デザイナ以上にデザインを熟知している人で、彼らがデザインを考えながら自分でクレイを削るのです。マツダは、そういう力を持つ人材を最大限に活用しています。
中村 なるほど。
延岡 別の言い方をすると、東大で電子工学を勉強したエンジニアよりも、現場でさまざまな材料に触れたりしている高専卒、高卒の人の方が、他社と差別化できる本当の価値を創ることができる可能性が高いと思うのです。そういう人材をうまく使うことがポイントですね。
中村 最近の流行りとしては、デザインスケッチから「Alias(エイリアス)」などのソフトウェアによる3Dデザインに入っていますよね。どのタイミングでクレイ・モデルが入るのか私にはよくわかりませんが、マツダでは「Alias」などを使ったりはしないのですか。
延岡 もちろん、いろいろな形があります。先ほどの話はスポーツカーのように、アーティスティックな部分が本当に評価される車種の例です。
戦略的に変えるべきこと、残すべきこと
中村 延岡さんもマツダのご出身ですが、最近のマツダはたしかに素晴らしいですね。
延岡 デザインが大きな力を持って価値を生み出しています。今日の話は価値づくりにおける設計と製造の分業・再統合が主なテーマですが、もう1つ、デザインとエンジニアリングの一体化による価値づくりも重要ですね。
中村 そうですね。
延岡 デザインとエンジニアリング(の関係)は非常にはっきりしていて、デザインとエンジニアリングが分業化したのは、1920年代に米GMに初めてデザイン部門ができてからのことです。
中村 (さまざまな階層に合った車種を提供するという)車型展開を行ったのがGMですね。
延岡 それで無理やりデザイナという職種を作ったのです。それ以前は、商品を設計する人が、建築家と同様に、デザインも含めて良いものを作るというスタンスで仕事をしていました。今、デザインが設計から分業して100年弱が経ちますが、最近では間違いなくデザインと設計の統合が進もうとしています。
中村 規模の問題もあるかもしれませんが、マツダは組織的にも他社とかなり違いがあるような気がします。
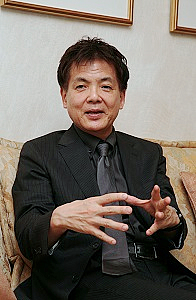
延岡 規模ですね、やはり。
中村 逆に、その規模が今はうまく機能していて、(組織が良い意味での)「中抜き」になっているのではないでしょうか。たとえば設計―生産技術―製造というラインの中で、設計と製造の結びつきがきわめて強いと私は思います。設計と製造の連携が良好で、もともと製品ラインナップも少なかったので、トヨタのように「車型が多いのでモジュール化した方がいいのか」という話にならず、今の時代に合ったアプローチが取りやすくなったのではないかとみています。
延岡 なるほど。
中村 というのも、先ほどのクレイ・モデルによる造形の話にしても、より大きな会社だと、一気にデジタルツールに流れてしまい、現場では、街中の3次元(の風景)をガリガリ描いて(バーチャルの世界で屋外に)飛び出した状態で、光の反射をCGで見るということを一生懸命やっているわけです。そういうことではなくて、昔からの淡々とした作業の積み重ねをやる人がまだ残っていることが、結果的にマツダの強みにつながったのではないかと私は思いますが、そこはどうお考えでしょうか。
延岡 単に残っているだけではなく、差別化のために戦略的に残していますね。
中村 戦略がある、と。
延岡 そうです。現場にものすごい力量を持ったスーパーマンが数人いて、彼らが引っ張っているのです。リスクもある尖ったやり方ではありますが、皆に才能があったので、たまたま当たっているという感じです。今、マツダではデザイン決定についても、多数のユーザにモデルを見てもらうユーザクリニックをまったく行っていません。自分たちが信じる普遍的な良いモノを作ろうというスタンスを貫いています。
中村 その意味で、マツダの事例は、日本のモノづくりにおける新たな価値づくりの参考になるのではないでしょうか。
延岡 もともと自動車産業は、価値づくりが比較的容易な業態です。本当は、日本の電機メーカから1社でもそのような企業が出て来てくれたら理想的なのですが…。でもそれは、まったく無理な話でもないと思います。アップル然り、ダイソンも、掃除機だけであれだけの利益を上げているわけですから。
中村 少々厳しいことを言えば、ダイソンの掃除機は吸引力を始めとする機能が、とびきり優れているわけではありませんよね。
延岡 はい。機能的価値で売れているのではありません。それでも僕は、2台も買ってしまったのですが(笑)
中村 そうなんですか(笑) やはり日本の電機メーカにも1社ぐらいは、そういう会社がほしいところですね。自動車やコピー機などでは、日本メーカが高い競争力を持っているのですが…。
延岡 あとは世界的なブランドになっているとすれば、非製造業ですが、無印良品もそうだと思います。
中村 無印良品はフランスなどでもかなり売れているようですね。
延岡 そうですね。
中村 話を戻しますが、今日は価値づくりの狙いやポイントに加え、主観的価値の汎用化、それから組織的能力をいかにマネジメントしていくかが、ベンチャー企業は別として、とくに既存の大手メーカの課題だという話を伺いました。
延岡 その前に、製造こそ価値を生む源泉であるということを、再認識してほしいと思います。おそらく、それが大事だということがわかっている人は案外多く、実際にクール・ジャパンがどうしたとか、有田焼や南部鉄器などの伝統工芸がどうという話をよく耳にします。でも私が言いたいのはそういう話ではなく、製造のメインストリームの部分で、日本のモノづくりの強みを活かした価値づくりをきちんと行っていこう、ということなのです。
中村 そうですね。私もそこには以前から違和感を抱いていました。経産省のミスリードによる部分もあるのではないかと思います。
延岡 経産省はおそらく、モノをどう作るかではなく、モノづくりよりも商品開発の方が大事だという方向に、持って行っていこうとしているのでしょう。その一方で、そう言ってはいながらも、クール・ジャパンのように、メインストリームのモノづくりから遠く離れた「飛び地」にあるような話ばかりをしています。そもそも日本企業が本当に誇るべきモノづくりの強みを、製造のメインストリームの中できちんと価値に結びつけようということを、誰も手がけていません。
中村 そう思います。手前味噌ですが、当社は第4回「日本モノづくり大賞」を経済産業大臣からいただいたのですが、私はその表彰状に「あなたをモノづくり名人として認めます」と書いてあるのを見て愕然としました。「『日本モノづくり大賞』の枠組みには職人しか存在しないのか、これは少し違うのではないか」と(笑)。
延岡 じつは私は、その「日本モノづくり大賞」の審査員を近畿地方でやらせていただいたことがありますが、政策的な意図をかなり感じますね。
中村 最後に、日本企業が価値づくりによって再生していくうえで、3次元CADやシミュレーションを始めとするデジタルエンジニアリングがどう役立つとお考えですか。
延岡 繰り返しになりますが、難しくはあっても、本当に価値を生むことを商品づくりの中に入れ込もうとするからこそ、効率化のための技術が要るわけで、デジタルエンジニアリングは日本企業の価値づくりに間違いなく役立ちます。デジタルツールを単なるコミュニケーションの道具ではなく、価値づくりを行う人が、いわばスーパーマンになるようなものにしていってほしいと思いますね。
中村 それは大事なポイントですね。
延岡 私が以前、3次元CADの研究をしていたときもそうでしたが、良い会社は3次元CADの導入時に役割分担に関する組織的な革新も同時にきちんとしていて、フロントローディング(製品開発の初期工程に重点を置いてリソースを投入し、品質の向上を図ること)もしっかり進めています。ところが、あまりよくない会社は、CADデータが3Dであるという価値だけを利用しているにすぎず、仕事のやり方や組織構造自体を変えようとしません。ですから、デジタルエンジニアリング技術を提供する会社には、クライアント企業が、仕事のやり方や組織構造自体を変えるというところまでを、ソリューションとして提供していただきたいですね。
中村 そうですね。デジタルエンジニアリングそのものが、付加価値を生み出すのではありません。私がこの仕事を手がけている理由は、デジタルエンジニアリングを、延岡さんがおっしゃる意味的価値を生み出す土壌にしていかなければならないと思うからです。逆に、デジタルエンジニアリングにすべてのリソースを投入してしまったら、意味的価値が高まらないどころか、同じことが誰にでもできてしまうようになってしまいます。
延岡 それでは差別化になりません。
中村 そもそもデジタルエンジニアリングでできることは、たかが知れています。その、たかが知れているところに過大な人的コストを投入していることが問題で、デジタルでできることはデジタルに任せるべきだと思うのです。むしろデジタルでできないことを、いかに人間がやるのかが大事であって、「人間ができることはいったい何なのか」と、ある意味で人間を追い詰めるのがデジタルエンジニアリングの役割だと私は考えています。そういう人間とデジタルとの戦いのようなものがなければ、向上はありません。
延岡 なるほど。
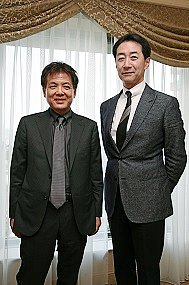
中村 加えて言うと、たとえば最適化であるとか、ある部分の物理的な仕様を出すといったことはコンピュータでできますが、それ以上の価値はコンピュータには出せません。だから「もっと高度なことや、意味的価値に結びつくようなことを、人間がやりなさい」という一種の対峙関係を作るものが、デジタルツールだと思うのです。いわば、人間を楽にするためのツールではなく、人間がより高いところを目指すための環境を作るものが、デジタルツールだと私は位置付けています。今まで人間が頭の中で漠然としかイメージできていなかったものが、バーチャル技術によるシミュレーションを見ることによって「じつはこういうことだったのか」という気付きを生むようなものに(デジタルツールを)していきたいと思いますね。今日は非常に興味深い話をいただき、ありがとうございました。
延岡 いえいえ、こちらこそありがとうございました。
取材・構成 ジャーナリスト加賀谷貢樹