第1回 進化せよ!日本の「モノづくり力」

「やってみなはれ」のスピリットを取り戻せ
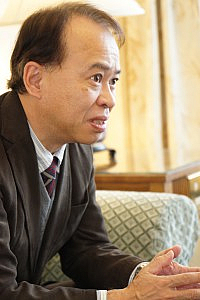
中村 一方、大手企業の動きを見ても、非常に残念なことが数多くあります。巨大な企業体を維持し、雇用を維持し、収益を上げて株主に対する責任を果たしていく
中で、経営が難しいのもわかります。とは言いながら、その中で目新しい戦略や動きを打ち出していくことができない現状を変えられないようなら、近い将来大きな問
題が起きるでしょう。
関 事なかれ主義や平均点主義が1番の問題でしょう。管理を強めていくと、結局そうならざるを得ないのです。「目立ってはいけない、でも仕事はちゃんとやりなさ
い」と言われたら、そこそこのレベルを狙って平穏無事に過ごすことになってしまいます。ソニーも、昔は「われわれはモノを作るのではない、市場を創るのだ」と、素晴らしいことを言っていたではないですか。
中村 おっしゃる通りです。
関 私はじつは、マーケットリサーチをあまり信用していないのです。モノづくりは基本的にプロダクトアウトだと考えています。百発一中、あるいは二中ぐらいしかヒットは出ないかもしれませんが、モノを生み出し、そこに爆発的なヒットを起こし、モノづくりを進化させていくということを、ソニーは実践していました。ソニーが今、かつてない苦境に陥っているのは、「真面目なる技術者の技能を、最高度に発揮せしむべき自由闊達にして愉快なる理想工場の建設」(東京通信工業株式会社設立趣意書)に代表されるソニーイズムがなくなってしまったからだと思います。
中村 そうですね。
関 NHK連続テレビ小説『マッサン』の主人公・亀山政春のライバルである鴨居欣次郎は、サントリー創業者の鳥居信治郎さんがモデルで、「やってみなはれ」が鳥居さんの口癖でした。サントリーにはそういう社風が受け継がれていると思いますが、企業の根底にある独自のポリシやアイデンティティが、株主至上主義などで相当薄められたのではないでしょうか。大企業も、尖ったポリシをもう1度取り戻し、「われわれはこれで行くんだ」という明確な特徴を持った企業になっていかないと、家電は韓国の下請けになり、自動車はドイツの下請けに甘んじてしまうことになるのではないかと危惧しています。こうした中、各社が特徴のある製品を作らなければならないのに、従業員たちがそれにふさわしい環境に置かれているのかどうか、大いに疑問です。
中村 具体的にはどういう環境に置かれているのでしょうか。
関 「出る杭は打たれる」ではなく、「出る杭」を伸ばしていけばいいのに、中間管理職あたりが押さえつけてしまうのですね。非常に厳しい言い方をすれば、仕事のできない中間管理職が仕事のできない部下を再生産しています。部下の尖った仕事ぶりを見て、「すごいじゃないか、もっとやれ」と褒める文化が薄れてきているのではないですか。
中村 関さんがおっしゃるように、最近、中間管理職の力が落ちています。加えて経営層も戦略面が弱いということになると、現場力でなんとか走らざるを得ません。そのため現場力の強さに頼り過ぎ、いわば経営層が戦略的に頭を使わない状態になってしまっているのです。
関 そうですね。
中村 なまじ現場力があるので、経営層がとくに何もしなくても内部留保が増加しています。だから、かえって余計なことには手を出さない。株主資本主義の弊害は大きいですね。
関 最近では、ローランドがMBO(経営陣による買収)を実施し、上場を廃止しました。それ以前にも、ヤマハリビングテックが、ヤマハとファンド会社からの出資分についてMBOを行い、トクラスという会社になりました。こういう選択を行う経営陣も出始めてはいますが、まだ少数ですね。
3Dデータを活用し「アナログのモノづくり」を極めよ
中村 ここまで、日本のモノづくりの現状について話をしてきましたが、ではモノづくりを強くしていく具体的なアプローチとしてはどんなものがあるのでしょうか。経営視点もありますが、足下としての現場力、モノづくり、生産という視点で何ができるかが大切です。中でも、デジタルエンジニアリングを始めとする新しい手法や考え方を応用し、新たなモノづくりを行う力を提供したり、支援していくことが必要だと思います。その鍵の1つとして、関さんがかねてから主張している3Dの活用についてお話いただけますか。
関 大手ではもう当たり前ですが、製品の設計については3D化が完全に主流になっています。 ただ悲しいことに、それが最後まで一貫しておらず、サプライチェーンの最終段階である廃棄まで含めて、せっかく3次元で作ったデータがどこかで2次元にトランスレートされていくのです。3次元CADで図面を描けば2次元図面はすぐできるので、現場では設計から2次元図面をもらい、それをNCデータに落としてマシニングを行っています。「なぜCAMを導入しないのか」と聞いても、わかっていただけないケースが数多くありますね。私がデジタルエンジニアリングという言葉を知り、実践したのが1999年ですが、今の日本はもう20年近くも2次元図面偏重から抜けきれていないような気がします。
中村 そうですね。
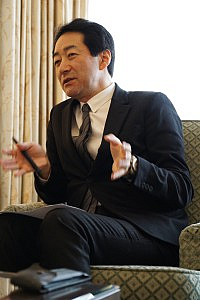
関 私は「3D一気通貫モノづくり」と呼んでいるのですが、3次元CADデータをトランスレートすることなく、そのまま組立現場なり部品製作、メンテナンスなどに活かすというのが私の考え方。これについてもまさに二極化状態で、すでにできているところもあれば、導入に拒否反応を抱いているところさえあるのが現状です。
中村 1かゼロ、すなわちオールデジタルかオールアナログで捉えているのではないですか。モノづくりの世界でも、デジタルもしくはメソッドで対応できることと、技能すなわち皮膚感や手業で対応できることは明らかに違います。それを十把一絡げにせず、モノづくりの力を分析的に区分けてアプローチすることの大切さを訴えていく必要がありますね。
関 これは昔から言っていることですが、私はアナログ技能のほうがデジタル技術よりも上位にあると思っています。アナログでできることはアナログでやればいいし、デジタルのほうがいいことはデジタルでやればいい。まずそこの区分けをしっかりすべきです。
中村 たとえばズームがついたデジタルカメラを使いこなすには、デジタルの力を借りなければいけませんが、写真を
見るのは人。同様に、考えるのも気付くのも人であり、それをアナログと言っているわけですが、デジタルとアナログは連携しなければなりません。さらに言えば、デジタルは、人間の限られた力を増強するものだと私は捉えています。
関 よくわかります。だから私は、モノづくりは結局「脳内アナログ感性」のなせる業であり、つまらない仕事はデジタルにやらせるべきだと言っているわけです。
中村 その通りですね。測るとか干渉を見るといった量的な部分はデジタルに任せればいい。一方、そこで気付きを得るとか、その気づきに対する判断や対策を行うことは人間の仕事であり、そこの切り分けをしなければなりません。その意味で私は、デジタルとは、人間に「気づき」を起こさせるための環境だと考えています。もちろんアナログでも気づきは起こるのですが、きわめて限定されるのです。たとえば人間の目で物が見える範囲は高々、限られているので、私たちは100メートル先で起こっている小さなことには気がつかない。
関 そうですね。
中村 100メートル先のことも、手元で起こっているがごとくに把握して、人間に気付きを起こさせるための環境がデジタルです。これは距離だけではなく、時間もあてはまります。データを10年前にさかのぼるとか、半年後に検知するということは人間には到底、できることではありませんから、デジタルの力を使うという位置づけですね。
関 カメラの例がわかりやすいですね。一昔前、カメラはデジタルよりもアナログのほうが上だと言われていましたが、ほぼデジタルに移行しました。アナログカメラはもはや一部のマニアのためのものだという話もありますが、ちょっと待ってほしいと思うのです。もともと写真とは、自分の好きな被写体を好きな構図で美しく撮るというアナログの感性の世界であり、そのツールがデジタルに変わっただけなのです。モノづくりも同様で、アナログのモノづくりが最上位に来ることに変わりはなく、それに対して、デジタルのパワーをどこに使えば効率的なのかということを、きちんと判断していくべきです。
現場力を高める「メソッド」を構築せよ
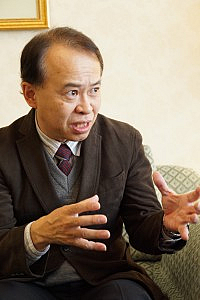
中村 デジタルツールと、人間のアナログな思考活動をどう連携させるのかということを議論するのが、デジタルエンジニアリングに関わる我々に課せられた大きなミッションだと思います。私は、人間の思考活動の中に、問題を解決していくための手法、すなわち問題解決メソッドがあり、そのメソッドを効果的に動かすために定量的な分析を行い、その対象を広げていくための役割としてデジタルツールが用いられるべきだと思います。われわれがやらなければならないのは、そのメソッドをいかに作り上げていくかということですが、残念なことに、今まではそういう活動が不十分であったと思います。現場活動において、論理的な思考行動が弱いPDCA(Plan―Do―Check―Action)はモノづくりにおける非常に重要で、日本がここまで成功してきたアプローチであるわけですが、PDCAの中ではメソッドが埋没してしまいがちになるのです。TPS(トヨタ生産方式)もメソッド化の試みの1つではありますが、外に見えているのはあくまで考え方や思想が本質であって、具体的なメソドロジー(方法論)は、少なくとも外部にはなかなか、見えてこない。
関 なるほど。
中村 だからデジタルを活用しながら、皆が何らかの運用ができるメソッドにまで落とし込むということを、われわれはやらなければならないのでしょう。
関 メソッドという言葉で今思いついたのが、タグチメソッドです。これは非常に素晴らしいメソッドですが、それをアナログでやろうとすると、かなり大変な話になります。理論的には4374通りの条件による試験結果を、たった18通りの条件で推定できるわけですが、18通りの試作品を作るのはとても無理だという話になりがちでした。でも今では、18通りの3次元CADデータを作ってシミュレーションにかけて、その中から良さそうなものを2種類ぐらい選んで試作すればいい。そういうことを今、進めていかなければならないのです。デジタル、3次元CAD、CAE(Computer Aided Engineering)というツールがあるからこそ、タグチメソッドという素晴らしいメソッドを皆が使えるわけですが、それがなかなか広まっていない。でも、そこに気付いている会社はすでに実践しています。
中村 なるほど。
関 それから、企業によっては「こういう試みがうまくいった」という情報を発信していますが、受け手の側に、その情報の素晴らしさを感じるリテラシーが欠落しているのかもしれませんね。
中村 タグチメソッドにしろTRIZにしろ、重要なのは、現場の従業員がその思考プロセスを運用していくためのナビゲーションを作ってあげる必要があるということです。「タグチメソッドは素晴らしい、でもそれを使って考え、造り上げていくのはあなたです」というように主体的に仕事を進めることができる環境。創造的な作業はできる人にはできるわけですが、そうでない人でもメソドロジーで展開できるような仕組み――創造に導くプロセスマネジメントを構築したいと思っています。
関 LEXERさんでは、生産工場をコンピュータ上で仮想化し、モノの流れや動きを予測する生産シミュレータの「GD.findi」を展開していますね。
中村 LEXERではとくにバーチャル(機能的にそのようであること)と言っているのですが、単なる3次元化やアニメーション化ではなく、こんな状況でこんな問題が生じた時に、こんな分析をしてこんな手を打ったらこうなったということを、バーチャルの中で、いろいろとシミュレーションしてみるわけです。私にとってバーチャルはリアルと同義です。A、B、C、Dという対策に対してどんな現象が起きたかを把握できれば、対策を打つことの意味と効果を理解でき、それが現場力の推進力となるのです。バーチャル環境で現場力を高める経験を通じて初めて、その手法の意義や「こんな使い方をすればいいのか」という理解につながり、そこから新たなアイディアが生まれていくわけです。今日のモノづくりが置かれている難しい状況では、こういう環境を作っていかなければ、従業員をしっかりインボルブ(関与)させることはできません。
関 メソッドを作っていく人材が非常に重要であるのはもちろんですが、何よりもそのメソッドをきちんと理解したうえで使っていくことが大事ですね。実際、エクセルに数値を入力すればすぐに解析の結果が出てくるわけですが、そのデータの意味がわからないという人が結構います。
中村 わかっていませんよね。
関 CAEもそうです。今、この話をしていて思い出したのですが、生産用のジグは製品の大きさによって、最大このぐらいの寸法だということが決まっています。ところが、たとえば受けジグは、多くの企業でいまだに1個1個設計しているのです。大きさもこのぐらいだとわかっているし、外形のデータは3次元CADから持ってくれば自動設計ができるので、いったん自動設計のプロセスを構築すれば生産準備のスピードは格段にアップするわけです。日本人なら、そこに気付く人がいると思うのですが、そういう人材がなかなか現れない。
中村 なかなか、そういうことができないですよね。
関 今、製造業に体力をつけることを目的に、3Dツールを活用するための基礎講座を担当していますが、公差解析やシミュレーションなどはまず手計算でやらせています。手計算でやって初めてツールが使えるのであって、私はそれをやらないと絶対に駄目だと思っています。理論を理解したうえでメソッドもしくはツールを使うことを教えていかなければならないのに、そういう教育ができていません。
中村 時代の変化にともない、エンジニアがやることが変わり、技術も変わっていく中で、理論をどのレベルまで押さえていくのかも重要です。私は理論と皮膚感に加え、それらの関係性をどう理解し、どう把握するかという、価値を見出す能力のようなものの醸成が重要だと思いますね。
関 大事ですね。
中村 一方、先にお話のあった治工具の話で言うと、アナログかデジタルかに関わらず、治工具を設計する考え方そのものを構築するための思考形態が必要で、それについて、モノづくり現場でも、何らかのアプローチや気付きが出てきてほしいところです。ある意味、以前はそういうことができていたのに、最近なぜできなくなったのかと考えています。単なる忙しさの問題なのか、それとも、そういう人材がいなくなっているのか…。決してそうではないと思うのですが。
関 そうは思いたくないですよね。たとえば生産技術の末端で働く従業員は「君の仕事はジグを作ることだ」と言われたら、「これが自分の仕事だ」とばかりに、新製品が立ち上がるたびに同じようなジグをいちいち設計し直しているのでしょう。本当は、そこに疑問を持たなければなりません。物事を逆方向から見ることができる人は、昔から少ないのでしょう。本当は、そこに疑問を持たなければなりません。物事を逆方向から見ることができる人は、昔から少ないのでしょう。
中村 私は時代が変わったとしても、人の素養はそう変わらないと思います。本人が今置かれている環境の問題ではな
いでしょうか。昔は今に比べて製品の種類が少なく、品質やQCと言っても、求められるレベルが今とは圧倒的に違います。したがって、昔はまだ仕事に余裕があり、自発的な活動もできたでしょう。ところが今は製品の種類も格段に増え、品質などに対する要求度が高まる一方、ローンチングの期間も短くなり、人も削られ、それでいて成果が求められています。そういう中で、何かを自発的にやれと言っても非常に難しくなっているのが現状で、私は経営側の問題が大きいと思いますね。
関 そうかもしれないですね。
中村 それから、これは時代の必然とも言えるのですが、仕事で与えられているスコープ(領域)が狭くなっているために、モノづくりを違うスコープで見る機会がありません。以前は自動車会社でも、プレス加工や塗装、組立を始め、さまざまな分野を熟知している人がいたのに、今ではそういう人がほとんどいなくなってしまいました。プレスはプレス屋さん、塗装は塗装屋さん、組立は組立屋さんと分業が進み、他分野の工程がわからず「プレスってどうするの」という状態になっています。(生産現場を)広い目で見ることができる人材を、もう一度育てることが必要でしょう。
関 先日面白い話があったのですが、アルミの削り出しで作る高さ4メートルの円柱に、設計担当者が±100分の5という寸法公差を入れてきたそうです。一体誰がどうやってそれを測るのかと(笑)。最近、実際にそういう人材が出てきてしまっているんですね。本人は「品質は高いほうがいいから」と言っていたそうですが、とても笑えない話です。
中村 そのような技術的な意義を指導できない状況なんですね (笑)。
関 私がローランド ディー.ジーでデジタルセル生産システムを手がけていた時、自分自身でやることは実はあまりなくて、むしろ工場の中を歩き回ることが仕事でした。何か言いたそうな人や、危なそうな作業を見かけた「ちょっとあそこの面倒を見てあげて」とスタッフに指示を出したものです。そういう役回りの人が、工場にいなくなってしまったのかもしれないですね。
「シミュレーション」で進化するモノづくり
中村 そういう状況は、1つは組織のあり方や経営の体制から生じていると思います。経営を変えろと言うことは簡単ですが、なかなかそうもいかない中で、何ができるのかをわれわれは考えていかなければなりません。今後の日本のモノづくりのあり方を考えるとともに、現状でも蓄積や力を大いに持っている日本のモノづくりをどうプロモートしていくのかという部分を、微力ながら担っていきたいと私は思っていますが、関さんはどうお考えですか。
関 私は「3D一気通貫モノづくり」を製品の切り口で見ていますが、それをモノづくり現場におけるシステムという切り口で見れば、中村さんのおっしゃるメソドロジー、すなわち体系的な考え方がやや薄いのかもしれません。私は「日本のモノづくり力はまだまだある」と話していますが、はっきり言って、このまま行ったら(新興国に)追いつかれるのは時間の問題です。その意味で、日本はこれからもっとモノづくり力を進化させていかなければいけません。そこでメソドロジーやツールを活用し、「この工場のこのレイアウトで、こういう流し方をしたら、本来どれだけ生産できるのか」といったシミュレーションを進めていくべきだと思います。
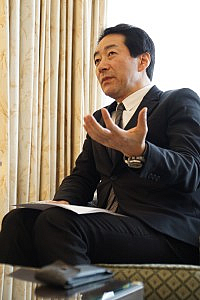
中村 そうですね。
関 日本では従来、その部分を「現場のカン」に頼ってきました。以前は経験豊富な人がいたので、「この製品ならこの人数でこう流せばクリアできる」というカンが見事に当たっていたのです。ところが、そういう人材が少なくなってきている今、「GD.findi」などのツールを使いこなし、「本来(うちの現場は)理論的にはこれだけできるはず」だということをシミュレートするのは非常に有効だと思います。
中村 デジタルエンジニアリングツールを活用するうえで、たとえば生産性を向上させるためには、こういうケースなら、どういう工程設計や編成、物流を行えばいいのかという、システムの組み方に関するノウハウの蓄積が必要ですね。
関 おっしゃる通りで、私は「GD.findi」に関する情報を得て気付いたのですが、3次元CADによる設計につきものであるデジタルモックアップを組立性評価に利用すれば、この設計なら何分で組めるという、いわゆる標準時間が見えてくるのです。それと「GD.findi」による生産システムのシミュレーションをリンクさせると、「この製品をこの仕組みで組めば、1時間当たり○個できるはずだ」というレベルまで、精緻な予測が可能になると思います。そこにぜひ持って行きたいですね。
中村 そうですね。われわれは製品そのものではなく、製品を作っていくための生産システムに関するコンセプトである「SIM(Simulation Integrated Manufacturing)」を提唱していますが、関さんがおっしゃる「3D一気通貫モノづくり」とSIMの軸は、じつは密接に関連しています。製品から来る軸が「3D一気通貫モノづくり」であり、生産システムから来る軸がSIM。この2つが常に並行して動いていく中で、良い製品なり良い生産システムができるということになります。そういう流れを作っていきたいですね。
関 その2つの流れが、どこかで1つの共通言語もしくは共通データとして、製品と生産システムをつなぐ場が出てくるはずです。
中村 加えて申し上げると、各ステージごとに気づき、対策、提案、検証があるわけで、それがPDCAとしてずっと回っていくのです。その中のワンステージで起きた気付き、対策、提案、検証を何らかの形で残しておきたいですね。そのあとのステージで、別の部署が手がけた前のステージで起きた気づき、対策、提案、検証を活かすことができます。あとのステージでやり方を変えるにしても、前ステージを手がけた人の意図を知らないと、さらなる作り込みができません。(各ステージで起きた)考え方や活動をアーカイブとして見える形にして、他部門もしくは他の事業所に伝えていく仕組みを作りたいですね。
関 作りたいですね
中村 エクセルファイルに検討ポイントだけが残るのではなく、検討ポイントの原因を参照しながら、「ここで干渉が起きる」とか「この編成でやると何人余ってしまう」、「設備の稼働率がこうだから、新しい製品を流したらこのロボットが止まってしまう」など、シミュレーションを使って現象的に確認したことを他部門の人が理解できることが重要です。そういう仕組みの中で、現場(生産現場ではなく現業)担当スタッフの活動を他の人が理解し、さらなるレベルアップを図るプロセスを回していきたいですね。それが知恵を集約するということだと思いますし、それをやっていかないと企業力が伸びません。
関 おっしゃる通りです。
中村 ある工場だけでやるのもいいのですが、今、多くの企業が海外展開も進めている中で、いわゆる兵站線が伸びて
切れかかっています。そういう中で、他部門や他事業部にテストデータだけを送るのではなく、現場体験を含めて知恵を共有できるシステムを構築することが、1本の太い補給線になると思いますね。
日本のモノづくりの知見をグローバルビジネスに
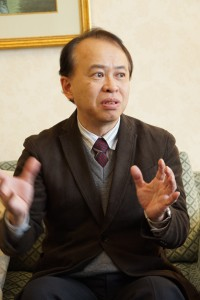
中村 さらに言えば、自社の強みを自社で使うだけではなく、ビジネス戦略として活かすことがポイントだと思います。
関 あり得ますね。これからはモノを売るだけでは駄目です。先に例に挙げたエンシュウも、同社が培ってきた技術やノウハウを活かし、トランスファーライン、製造設備を売っています。日本の生産システムは世界で引っ張りだこになるはずなので、これを売っていくべきだと思うのですね。「御社の現場に、当社のこの自動化設備を入れると生産性が何10%向上します」というように、生産シミュレーションを行い、その結果を出してプロモーションすれば説得力が増します。いつまでにどのくらい投資が回収できるのかもほぼ計算できるので、そこできっちり外貨を稼いでいくことが、今後日本のビジネスモデルの1つとして伸びていくような気がします。
中村 それがある意味、日本がこれまでモノづくりで培ってきた知見を売っていくという、新しいビジネスモデルになるでしょう。もっと言えば、私は生産システムのデザインだけでなく、運用管理もビジネスになると思っています。たとえば加工機、もしくはさまざまな装置を組み合わせ、制御系がつながった1つのセットアップとして、運用管理を含めてとくに東南アジアに展開していくのです。MES(Manufacturing Execution System)で状態をあたる、モノを流していくためのスケジューリングを行う、もしくはそれに対する検証・指図をするといったこともクラウド上で可能な時代になっています。
関 そうですね。
中村 今、製品力、マーケティング力、販売力を含めて皆が苦労している中で、日本が持っている力を活かす1つの出口戦略として有効だと思いますね。とくに今、東南アジアや南アジアで、欧米流のモノづくりで行くのか、日本流のモノづくりで行くのかという色分けが始まりつつあります。たとえば東南アジアには、TPSやカイゼンに代表される日本のモノづくりを追いかけようという人たちがいる一方、堅固な設計力から来るドイツなりヨーロッパのモノづくりを目指そうという人たちも出つつあるのです。
関 なるほど。
中村 そして、そのドイツも東南アジア市場を、ドイツ流のやり方に巻き込もうとしています。その典型「Industry4.0」で、それはまさしく世界のモノづくりをドイツ流に変えていこうという戦略の一環でもあるわけです。世界中がリスペクトしている日本のモノづくり力を世界に広めることを如何に日本の国策にするかを考えた時、単にモノを売るのではなく、生産システムの運用そのものを売ることも考えていくべきではないでしょうか。ドイツはすでに、その部分に対する仕掛けを始めているのですから。
関 完全に国策ですね。自動車のボディ剛性に関わるレーザー溶接技術の推進にしても、ドイツの国策です。かたや日
本は国策として、モノづくりに関して何をしたかと言うと、いつも補助金の話になってしまいます(笑)。
知恵の共有で日本の「モノづくり力」はさらに強くなる
中村 いずれにしても、企業が内部からなかなか変わることができない以上、外部にいる我々が強いメッセージを発信していかなければなりませんね。
関 私は先日フェイスブックで、3次元データを2次元データにトランスレートすることなく、サプライチェーン全体で使い倒すことが求められている今、なぜエンジニアリングの専門誌が2次元図面に関する連載を開始するのかというメッセージを発信しました。記事を投稿してから大きな反響があり、5、60件のコメントが寄せられました。強いメッセージを発信すれば、真剣に考えている人たちは集まってくるのです。われわれのような立場にいる人間が、知恵をどうやって集めてくるかが問われていると思いますが、SNSを使うと案外面白いかもしれませんね。
中村 今、私が興味を持ち、やりたいと考えていることの1つが、まさにそれなのです。日本企業は大手を含めて、現場の連携が非常に弱いと思いま
す。日本の技術者たちは企業に属していて横のつながりがなく、お互いに何をやっているかわからない。だから横のつながりをより密にしていく必要があると思うのです。
関 そうですね。
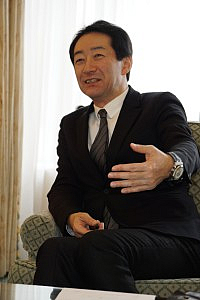
中村 モノづくりの手法から、現場へのアプローチ方法に至るまで、踏み込んだ議論の場やノウハウ、知恵を共有できる場があってもいいのではないでしょうか。モノづくりのリソースを活用するという意味ではなく、知恵を共有する仕組みを、モノづくりの世界で作りたいと思います。文字列だけで共有するのは難しいので、バーチャル技術を使いながらその意味を理解できるような、知を共有する世界を作っていきたいですね。
関 先のフェイスブックの記事にコメントを寄せた方の中に、技術士の方がいて、「非常に盛り上がって面白い。リアルに集まって議論する場があってもいいのではないか」と書き込みを下さいました。SNSで盛り上げておいてから、1度リアルの場に集まって議論しようということも、知恵の共有の場としてはありですよね。
中村 ありですね。
関 シミュレータを用意し、実際にデータを入れて相手のノウハウをシミュレートし、生産性がどれだけ向上するかを見てみるのも面白いですよね。
中村 セル生産やTPSの1個流し生産といった手法に関するノウハウをシェアしてもいいわけですよね。個々の製品の意匠や知財に関わるものではないわけですから、そういうものは徹底的にシェアし、お互いに利用し合うべきですね。工程設計ライブラリを作り、自由に使ってもらうという仕組みがあってもいいと思います。
関 私はローランド ディー.ジー時代に立ち上げた「デジタル屋台(D-Shop)」を他社にも公開しました。数千人に上る見学者を受け入れ、見学に訪れた企業がデ
ジタル屋台を始めたら現場を見せてもらうという約束で、写真やビデオの撮影も許可したのです。ところが、約束を守ってくれた企業は6、7社にすぎませんでした。見学に訪れた企業が「デジタル屋台」を始めた話を耳にして、担当者に電話をしてみると、「すみません、上司が現場を見せてはいけないと言っているので」と言われたケースが数多くあるのです。
中村 そうなんですか。
関 それでは駄目ですよね。その一方で、私に現場を見せてくれた企業からは、「こういう考え方もあるのか」と参考にさせてもらったことが数多くあります。そういう気づきを通じて、こちらもまた伸びていくのです。こうした知恵の共有の中で、日本のモノづくりは体系的にもっとレベルを向上させていくことができるでしょう。そんな仕組みが本当にほしいと思いますね。
中村 はい、その通りと思います。今後もモノづくりの将来について引き続き議論し、皆さんに問いかけていきたいと思います。関さん、今日は本当に有難うございました。
関 こちらこそ、深い議論ができてとても楽しかったです。有難うございました。
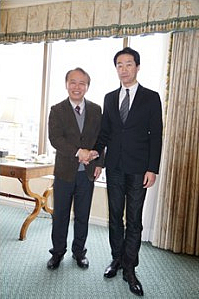
取材・構成 ジャーナリスト加賀谷貢樹