第2回 「グローバルなモノづくり」とは、世界を見据えた「ト ータルなモノづくり」と考えよ 前編

バーチャルとリアルの世界を統合
中村 ここまで、デジタルエンジニアリングのお話をさせていただきましたが、当然ながらデジタルエンジニアリングですべてのことができるわけではありません。人間の持っている力をどう組み込んでいくかということも大切だということが、2番目の話題になると思います。
鳥谷 そうですね。デジタルエンジニアリングの結果を判断し、どう生かすかはあくまで人間です。
中村 デジタルエンジニアリングでできていることは当然限られているわけで、デジタルエンジニアリングで現状できていないこと、さらにこれからやるべきことを、われわれとしては考えていかなければなりません。そのあたりについて、鳥谷さんの技術だけに限らず、いわゆる「製造IT」が置かれている現状と課題に加え、今後進むべき方向性についてお話しできればと思います。
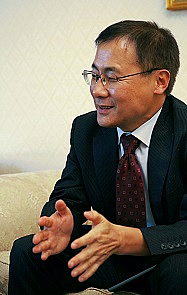
関 なるほど。
鳥谷 手前味噌になりますが、われわれの取り組んでいる超大容量の3次元データに関しては、じつはまだ解決されていない問題が数多くあるのではないでしょうか。まず、第一に超大容量データを利用した先進技術を三つ紹介したいと思います。一番目は部品間の干渉計算です。干渉についてCADで見るというレベルでは、みなさんが干渉計算を行っていると思いますが、大規模アセンブリ上での干渉計算は、じつはあまり行われていません。CADでは計算に時間がかかったり、大規模モデルが扱えないということで、なかなか行われていないのが実態です。ところがXVLの技術を使うと、超大容量の3次元データの処理も可能になるので、そういう強みをいろいろな場面で活かしています。二番目が制御ソフトの3Dモデルを利用したデバッグです。製造部門では、PLC(Programmable Logic Controller)を利用して製造装置を制御していますが、この制御を、装置の実機がなくてもXVLのモデルの中でシミュレーションできる「VMech(ブイメック)」というソフトを開発しました。従来は、製品の量産立ち上げをする際、制御ソフトがないためにラインの立ち上げができないというように、制御ソフト開発が生産のボトルネックになるケースがあったのですが、そういうことが可能になると、ラインの設備ができる前に制御ソフトのプログラムデバッグに着手できます。このような流れで、ラインができたら設備がそのまま動くというようなモノづくりをしたい、というお客様が結構いらっしゃいますね。
中村 なるほどね。
鳥谷 先ほど中村さんがおっしゃったように、日本企業では生技の力が強く、製品を世界中で生産していても、設備は全部日本で作っていることが少なくありません。今後そういうケースにシミュレーションが有効になってきます。加えて、世界中にその設備が設置されるとなると、そのメンテナンスをバーチャルで行う機能も非常に有効になります。まさにデジタルエンジニアリングの出番ですね。
中村 そうですね。
鳥谷 三番目はエレキのモデルとメカのモデルを合体し、メカ・エレキのハイブリッド検証を行うというものです。そうすると、エレキのモデルのほうから導体か絶縁体か、電位差はどの位あるかなどのエレキ属性が全部来ますので、解析をかけると「この辺でショートする」とか「この辺で静電気が起こる」ということが、デジタルモデル上で計算できるようになります。その結果、実物ができた後に実験しなければならない事柄が大きく減り、非常に迅速な製品開発が可能になります。
中村 そうなんですか。
鳥谷 実際に図研さんと開発した「XVL Studio Z」を展開してみると、いろいろ面白いことがありました。一般的には、メカ設計者とエレキ設計者が別々の部門で仕事をしています。ところが社内に組織のカベがあり、コミュニケーションがうまく取れていないことが結構あるのです。そのため、メカ設計者が開けた穴が原因で、回路がショートする可能性が生じる、というような問題が起きていました。通常は、メカ設計は終わっているので、後はエレキ側で解決してくれとなるのですが、「XVL Studio Z」で、電気の流れる道がメカ設計者にも見えるようになったお陰で、双方の組織がコラボレーションできるようになったのです。
中村 なるほどね。
鳥谷 そういう異分野のデータを統合し、よりサイズが大きくなった大規模データに対して、さまざまな検証を行っていくということが重要になっています。今後日本の製造業では、エレキ、メカ、ソフトウェアの部門が連携して動くようになっていくでしょうから、そこでデジタル検証の役割がますます大きくなっていくでしょう。
中村 PLCの制御シミュレータと、ハードウェアのシミュレーションソフトが、まだつながってないということですよね。
鳥谷 そうなんです。
中村 別々ですよね。制御される対象の機器は連続時間で動作するわけですが、離散系、連続系が統合された検証技
術はまだ確立されていないですよね。仮想で動くバーチャル製造機、もしくはスマートマシンのような話になりますが、その技術自体がまだできていないという状況だと思います。
鳥谷 次に、第二のポイントは、バーチャルとリアルの統合が必要になってきているのではないか、ということです。これには2つやり方があって、1つはバーチャルにリアルを取り込み、もう1つはリアルにバーチャルを取り込むわけです。レーザー計測機で空間を3次元スキャンして点群(3次元座標を表す多数の点の集合)化すれば、現地現物の3次元形状データを、バーチャルであるXVLに取り込むことが可能です。昨年、現物を測定した大容量の点群データを軽快に処理できる「XVL InfiPoints」という製品を、パートナのエリジオンさんと共同開発しましたが、工場のような数十億点規模の点群にXVLの大規模モデルを統合し、さまざまな検証が行えるようになりました。
中村 すごいですね。
鳥谷 それを、どんな場面で使うかなのですが、たとえば今、原発が止まっていて電力が足りないので、工場に自家発電の装置を入れたいというケースが考えられます。ところが工場の中には、階段はもちろん、さまざまな設備が所狭しと並んでいるにもかかわらず、正確な図面がありません。そこで工場の構内をレーザー計測し、装置は本当に入るのか、搬入の際に階段は邪魔にならないのか、どういう手順で設置したら効率的なのかということを、デジタルモデルで検証できるようにしたのです。調べてみたら、いろいろと適用範囲がありまして、工場も同様ですが、社会インフラなどのように長期間にわたって使う施設で、その中身の設備を効率化していく必要のあるケースなどに、非常に出番がありそうなのです。
中村 なるほど。
鳥谷 もう1つの例をあげましょう。ある造船会社の方から聞いたのですが、船は積み荷が空のときなどにバランスを崩すので、バラスト水と呼ばれる海水を船内に入れてバランスを保っているそうです。ところが、たとえばタンカーを例に挙げれので、バラスト水と呼ばれる海水を船内に入れてバランスを保っているそうです。ところが、たとえばタンカーを例に挙げれば、船が別の海域に移動して石油を積む際、バラスト水を捨てるのですが、それが原因で生態系が破壊されるという問題が起こっています。そのため、バラスト水中の水生生物を一定基準以下にして排水することが求められていて、古い船にはバラスト水処理装置を設置しなければならなくなりました。そこで船内の空間を3次元スキャンして点群化し、バラスト水処理装置をどうやって搬入するのかをシミュレーションするなど、いろいろな出番があると思っています。
中村 バーチャルをリアルに取り込むほうは、どうなっているのですか?
鳥谷 こちらはキヤノンITソリューションさんと一緒にやっているのですが、MR(Mixed Reality)システム「MREAL(エムリアル)」という製品があります。MRとは現実世界と仮想世界を融合させる映像技術で、バーチャルモデルのCG映像を現実の映像と合成し、HMD(ヘッドマウントディスプレイ)に表示させるのです。たとえば車の3次元モデルのCG映像と実車の映像を合成し、網の目のように張り巡らされたエレキの配線の3Dモデルが、現実の車の中にすけて見えるということも可能になるわけですよね。
中村 そうなんですか。
鳥谷 実際に(配線の)作業を行う場所に手が届くのか、どうすれば作業ができるのか、作業の際にこういう場所で腰が曲がって苦しくないのか、というところを本物の人間が仮想モデルの中で体験できてしまいます。
中村 今、工場や造船の例についてお話いただきましたが、実は正しいデータが案外なかったりするのですよね。
鳥谷 ああ、そうなんです。
中村 とくに工場などがそうですよね。
鳥谷 カイゼン、カイゼンで、どんどんレイアウトが変わってしまいますから。
中村 ですから、お客様の工場に行って「工場図面はありませんか」と聞くと、「ありません」と言われてしまうのです。それも、設備屋さんが勝手にレイアウトを変えてしまっている、などの理由で。
鳥谷 でも逆に、日本の現場力を活かし、カイゼン、カイゼンでそうなっている部分もありますからね。
中村 はい。そういう運用をせざるを得ないのです。現場力やカイゼンが日本の力だとしても、(その結果生まれた工場のレイアウトに関する)データは消失してしまうという状況ですから、その点ではレーザー計測と3次元技術を活かすことで、キャッチアップが可能だということですね。
鳥谷 まさにそういうことですね。
中村 そういう新しいやり方をすれば、現合(げんごう)合わせではなく、3次元データを活用し、あらかじめ予測を立てながらPDCAを回していくこともできます。外から見ると、デジタルで何でもできるように思えるのですが、実際にはまだできていないことが数多くある、ということですね。
鳥谷 技術的には可能であっても、現場に定着させていくのは本当に大変です。
中村 それを1つひとつ追っていかなければならないということだと思います。先ほど3次元データの活用についてお話をいただきましたが、業務プロセスという観点でそういう技術を有効に使っていく必要があるのはもちろん、エンジニアリングもしくは製造ITについて、まだできてないことがたくさんあると私は思います。
鳥谷 なるほど。業務プロセスという観点というところをもう少し説明してもらえませんか。
エンジニアリング・チェーンとサプライ・チェーンの連携

中村 おそらく鳥谷さんもそうだろうと思いますが、エンジニアリング・チェーンを、上流から下流までいかにデジタルデータで一気通貫させていくかということが、われわれの1つの大きなポリシでありコンセプトです。鳥谷さんと私が少し違うのは、鳥谷さんのところが製品軸での一気通貫であるのに対し、当社がプロセス軸での一気通貫であることで、両方の軸が並行して動いているというイメージです。もう1つ、私の立ち位置としてはエンジニアリング・チェーンなのですが、生産、製造においてさまざまな情報が連携していく中で、サプライ・チェーンの視点はどうなのかということも考えてい
かなければいけません。エンジニアリング・チェーンありきでもなく、サプライ・チェーンありきでもなく、どちらも重要で、それぞれが持っている情報に有効性が当然あるわけです。それらがいかに連携するかが大切であると思います。先ほど鳥谷さんがおっしゃった制御の領域、物理の領域と電気の領域を連携させることと同様に、サプライ・チェーンとエンジニアリング・チェーンをどうやって同期させていくのか。これは、ある意味で予定調和的な活動になっていく必要があると思いますが、そういう点でXVLの技術や、われわれが推進しているシミュレーション技術を活かしていけたらいいですね。
鳥谷 そうですね。XVLの技術でいえば、図研さんとやっている「visual BOM」が二つのチェーンの結節点に当たります。中村さんのお話のポイントは、もっと上流での検討が大事なるということでしょうか。
中村 最初に鳥谷さんもおっしゃいましたが、何をどこでどう作るのかという製品コンセプトや原価モデルなどが明確になってから、設計を起こし、量産プロセスに入っていくという流れがあるわけです。そういう上流の段階から、後工程で連携してくるサプライ・チェーン情報も、やはり上流の段階で、程度の議論はありますが、組み込んでおかないと。
鳥谷 なるほど。
中村 エンジニアリング・チェーンだけで考えたときのプランの過不足を検証しながら、サプライ・チェーンの視点で製品を作り込んでいく、という流れが必要です。その意味で、今までは、サプライ・チェーンとエンジニアリング・チェーンが別々に動いてきた中で、量産段階で双方の視点を調整しながら量産に入っていくというのが、日本企業におけるすり合わせの1つの側面でもありました。私は、仮にすり合わせが必要だとしても、量産に入る手前ではなく、もっと早い時点ですり合わせを行うべきだと思います。現場の方には申し訳ないのですが、量産直前のすり合わせは、いわば手戻りであり、そこでカイゼンが起きている以上、カイゼンはある意味で手戻りだと言っているのです。たしかにカイゼンは重要で、やらなければならないことですが、手戻りなのですから、本来はやらなくてもいいことで、やってはいけないことなのです。理想的には、一発OKが1番いいわけです。
鳥谷 それは当然ですね。
中村 一発OKができないからやっているだけなので、必要悪だと言ってもいいかもしれません。ただ、問題が出るのは事前にわかっているのだから、量産直前ではなく、あらかじめ事前にすり合わせて作り込んでいく必要があると思うんです。
鳥谷 なるほど、フロントローディングで、事前に問題をつぶすということですね。
中村 そこのギャップが非常に大きいですね。その点をふまえて、サプライ・チェーンとエンジニアリング・チェーンを早い段階で検証するには、広い意味でのシミュレーションが必要です。われわれは生産の観点で話していますが、生産シミュレーション技術を用い、エンジニアリング・チェーンの上流、もしくはサプライ・チェーンの上流と言ってもいいのですが、その時点でシミュレーションをかけて、どこで問題が出るのかを早い段階でチェックし、コンバージェンス(収束)させるのです。そういうアプローチが、これから製造に求められるようになってくると思っています。デジタルエンジニアリングがまだ下流にまで十分に通じていないという現状がある中で、どんなタイミングでそういうアプローチが有効になるのかはわかりませんが、そういう大きな流れは間違いなくあります。
鳥谷 下流にとってデジタルエンジニアリングが重要な意味を持つためにも大事な点ですね。
中村 そういう観点で、エンジニアリング・チェーンとサプライ・チェーンという、視点が異なる動きの連携を促進することが、デジタルエンジニアリングツールの大きな役割。それによって全体的な業務プロセスが変わっていくという意味でも、非常に重要なアプローチだと思っています。
鳥谷 なかなか高尚なお話ですね。われわれはもう少し、分かりやすいところを手がけています。たとえば、全自動でパーツカタログを制作できる「CATALOGCreator」というソフトを、われわれのパートナが作っています。パーツカタログに必要な情報は、部品の分解図とその部品に対応するパーツ番号、そのパーツに対する問い合わせ先などで、それらが表になっていればいいわけです。3次元の形状データは設計が作るわけですが、各部品のサービス情報はサービス部門などが持っているわけで、それらの情報構造は当然、設計部門が作ったエンジニアリングBOMのデータ構造とは異なります。ただ、共通のパーツのIDを持っているので、自動的にデータの関連付けが可能です。そういうやり方でサービス側の情報と、上流の設計情報を組み合わせて、2次元画像も3次元モデルも表示可能なパーツカタログを全自動で作成できる仕組みを整えました。これは今、非常に好調に引き合いをいただいています。
中村 そうなんですか。
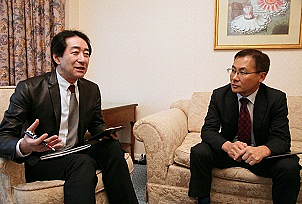
鳥谷 これはドイツのTIDというパートナが開発したのですが、かなり大胆な発想に基づいていて、「設計変更が起こったらどうするんだ」と尋ねたら「何も考える必要はない」と彼らは言うのです。設計変更が起こったら全部自動で作り直せばいい、あとはチェックするだけ。そこでOKだったらグローバルに配信する、という発想です。
中村 修正ではなくリビルドをかけよう、その波及はどこにあるかは気にしなくていい、ということですね。
鳥谷 そういう考え方です。たしかに今、カスタマイズ製品が多くなっていて、そうすると、お客様ごとにパーツカタログも異なります。そういうときに「CATALOGCreator」のようなソフトがあると、個別のお客様に合った汎用製品のパーツカタログを自動的に作成できますから、非常に安い運用コストで高いレベルのサービス構築が可能です。
取材・構成 ジャーナリスト加賀谷貢樹