第3回 エンジニアリングチェーンを強化し、価値と競争力 の再構築を図れ 中編

コンセプトとインテグレーションに弱い日本の製造業
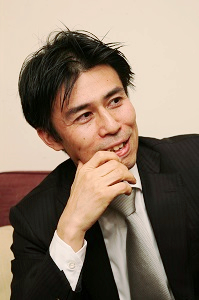
中村 まったく同意見です。日本が一番弱いのはそこですね。先日も海外の方と、ヨーロッパとアメリカと日本の製造業では何が違うのかという話をしたばかりです。
ヨーロッパはコンセプトが優れていて、インテグレションとオペレーションが弱い。アメリカは、コンセプトはあまり優れていないが、インテグレーションが強くオペレーションは弱い。一方、日本が強いのはオペレーションだけだとお話しました。
松本 なるほど。そういう切り口ですね。
中村 それは客観的に見て、あながち間違ってはいないと思います。例えば自動車で言うと、ヨーロッパでは設計図面通りに精度よく作られているものが良い製品だと考えるが、それに対し、日本では現場合わせで調整して製品の仕上がりを追求する、だが、図面通りになっていない。そういう違いがありますね。
松本 なるほど。今のお話を聞いて納得するところが非常にあります。だからこそ、自分はこの仕事をしているのだという思いが、本音の部分ではあるのです。
中村 そうですか。
松本 いまの話と似たようなケースですが、あるメーカでお客様に納入した機器の扉がずれていたことがあります。上役の方から「非常に恥ずかしい。現物の写真を見たが、とてもうちの製品とは思えない」という話を聞きましたが、同社はその不具合を、製造ミスや組み立てのミス、あるいは搬送中の振動による影響や包材の不良などの方向で原因付けようとしていました。そのときわれわれが思ったのは、誰がやっても確実に組み付けられるような設計をし、製品をどんな形で運んでも大丈夫なように梱包設計をすべきだということです。エンジニアリングの部分でしっかりそういうことをやっておけば、後工程で余計な調整や努力をする必要がありません。だから「この問題は製造不具合ではなく、設計不具合である」と、われわれは意見を述べました。奇しくも、この対談の中で、われわれが手がけていることの原点や価値に改めて気付かされたような気持ちです。
中村 それは日本のモノづくりにおける、きわめて特徴的な一面だと思いますね。別の言い方をすれば、それはカイゼン活動、すなわちPDCAサイクルの限界かもしれません。QC活動では現象的な問題に重きを置かれがちになります。だからPDCAサイクルを回すだけでは、そこにたどり着かないのです。PDCAサイクルはもちろん重要ですが、その背景に潜む本質的な問題に対する分析的なアプローチが弱いですね。これがQC活動やPDCAサイクルの問題点であり、日本人が一番苦手としていることなのです。
松本 なるほど。
中村 実際、製造現場で起こる不具合には、技能や工法、生産技術や設計に加え、それらが複合的して起こる問題な
ど、いくつかの背景があるわけです。ところが「いま起こっている不具合はそもそも、何が原因になっているのか」という原理的なアプローチが弱いですね。ましてや、先ほどの現場合わせを典型に、設計の問題に生産技術や製造部門で対応てきた歴史があるわけです。
松本 加えて、問題解決の方法を身近なところで模索しようとするだけで、別の方向でも考えていこうとする広がりがありません。ある限られた空間でしか物事を考えていないことの弊害が大きいと思いますね。
中村 もちろんカイゼン活動が悪いと言っているわけではないのです。カイゼン活動を行う中で、不具合や課題の本質を見出す視点や活動を入れたうえで問題点を切り出せば、カイゼンでやるべきことと設計でやるべきこと、生技でやるべきことが明らかになるのです。ここにエンジニアリングチェーンの強化、もしくは松本さんがおっしゃるように、エンジニアリングの視点で、上流の段階でおさえておくべきことを明確にするためのソースがあります。
松本 それができていないのは、自分の意識を、いまの自分の立ち位置にしか置いていないからだと思いますね。それを上に引き揚げ、全体的に俯瞰するような視点を持てば、「ここをやればいいんだな」とか「ここにも問題点があったのか」というポイントを発見し、さまざまな分野の解決策を集めて「このようにやっていこう」という方針が見えてくるような気がします。
現場に「気付き」を起こさせる仕組み
中村 そこは教育の話にもなるので、比較的、ハードルが高いかもしれません。現場の人たちに「いま起きている個々の問題について、どんな可能性があるのか」ということを気付かせる仕組みが要ると思います。
松本 そうですね。
中村 その際、「測る」とか「確認する」という部分でツールをどう使うかという課題があります。例えば、過去の製品の構造や生産プロセスの実績を計画に対して比較してみると、いま製造現場で起きている問題について「ここがずれているからこういう現象が起きている」という可能性も見出せます。シミュレーションを行うこともそうですね。これが原因だとは必ずしも言えないにしても、「ひょっとしたら、こういう可能性もあるのではないか」という「気付き」を現場に関わっている人たちに起こさせることが、われわれの基本的なコンセプトなのです。これを「気付きのイネーブラ(可能にするもの)」と言っています。
松本 気付きを起こさせる仕組みですね。
中村 はい。気付きは本体、本人の意識が相当高く、経験がなければ起こらないものです。それゆえ、教育と言えば教育とも言えるのですが、気付きを起こさせる環境を作り、その中で人を育てるための仕組みが必要なのです。現場は「目盛り」、つまりエンジニアリングにおける評価の視点が何もないまま活動しています。だからモノの企画・設計の中で起きた問題に対して「目盛り」で測って、さらに「目盛り」をよく見えるように拡大してあげて、対応しようというわけです。その「目盛り」を基準に、どの軸で問題が起きているかが見出せれば「こういう方法でやってみよう」という活動につながるでしょう。そういう評価の視点を与えることで、気が付く人は気が付くのだと思います。
松本 そうですね。
中村 そういう仕組みを、エンジニアリングのシステムとして確立すべきです。たんなる現場のカイゼンツールではなく、上流でエンジニアリング情報を定義して下流に渡し、現場で起きたことに対する比較や分析を行う仕組みがあることで「気付き」が起きるのだと思います。そうなれば、松本さんがおっしゃるように、自社が「どういう視点で何を作るのか」という明確な方向性を、上流できちんと打ち出せるようになるでしょう。
松本 いまの話とも関連しますが、昨年、山形県に本社を置く射出成形金型メーカの安田製作所(現・株式会社IBUKI)に出資を行い、私が同社の社長として経営に参画しました。そこで同社の社員に「金型製造の中で価値ある工程はどこですか」と尋ねたら、「1つは設計で、もう1つは仕上げです」という答えが返ってきたのです。設計の重要さは言うまでもないですが、金型はさまざまな部品が集まって1つのアッセンブリになっていて、仕上げ部門の人たちは、部品を組み立てていくときに、ボルトの締め方とか締め付けの強さを含め、手の感触をもとにして全体を仕上げていくのです。
中村 ボルトを締める順番もノウハウの1つですよね。
松本 そうですね。彼らは金型を組み立てるときに微妙な調整を行っていて、私はそういうことは設計できちんと定義すべきことだと思うのですが、「それは仕上げの仕事です」と言うわけです。場合によっては、仕上げの段階で何か不具合があったら、担当者の判断で削ってしまったりする。もちろん設計にフィードバックはしますが、それほどのことを仕上げ担当者が現場でやってしまうのです。中村さんは先ほど、ヨーロッパの自動車メーカが設計通りのモノづくりを行う一方、日本のメーカは現場合わせをしてしまうとおっしゃっていましたが、まさにその典型例です。
中村 そうですね。
松本 とはいえ日本のものづくりも徐々に、仕上げ工程に依存せず、設計の指示通りに作ればモノが仕上がる方向に変
わっているのではないでしょうか。 ところが、いまだに仕上げという後工程ですり合わせをしながら完成度を高めていく金型業界と、キヤノンやトヨタといった大企業の金型部門を比較すると、IT化と標準化が進んでいる度合いが決定的に違うのです。 中小の金型メーカは可視化はおろか、IT化も標準化もあまり進んでいません。一方、大企業の金型部門は可視化、標準化、IT化がどんどん進んでいますから、良い設計が出てきてそれが標準になる。当社では、「標準化の取り組みはチャンピオン化の取り組みです」とお客様に話しています。
中村 なるほど。
松本 チャンピオンスペック、チャンピオン手法、チャンピオンデータを使って設計を行い、それを手順書にまとめてITに入れていく。シミュレーションも活用しながら、そういうことを上流でどんどん行い、出来上がった図面の通りにモノを作る努力をしてきた会社と、いつまでも職人に依存している会社の差を、いま非常に見せつけられています。
中村 製品のバリエーションが増え、カバレッジを広げていかなければならない中で、これまでのように現場で調整を続けていくことには限界があります。CAE(Computer Aided Engineering)やシミュレーションを活用していくことは、間違いなく必要になります。
2 / 4