生産革新コンサルティング
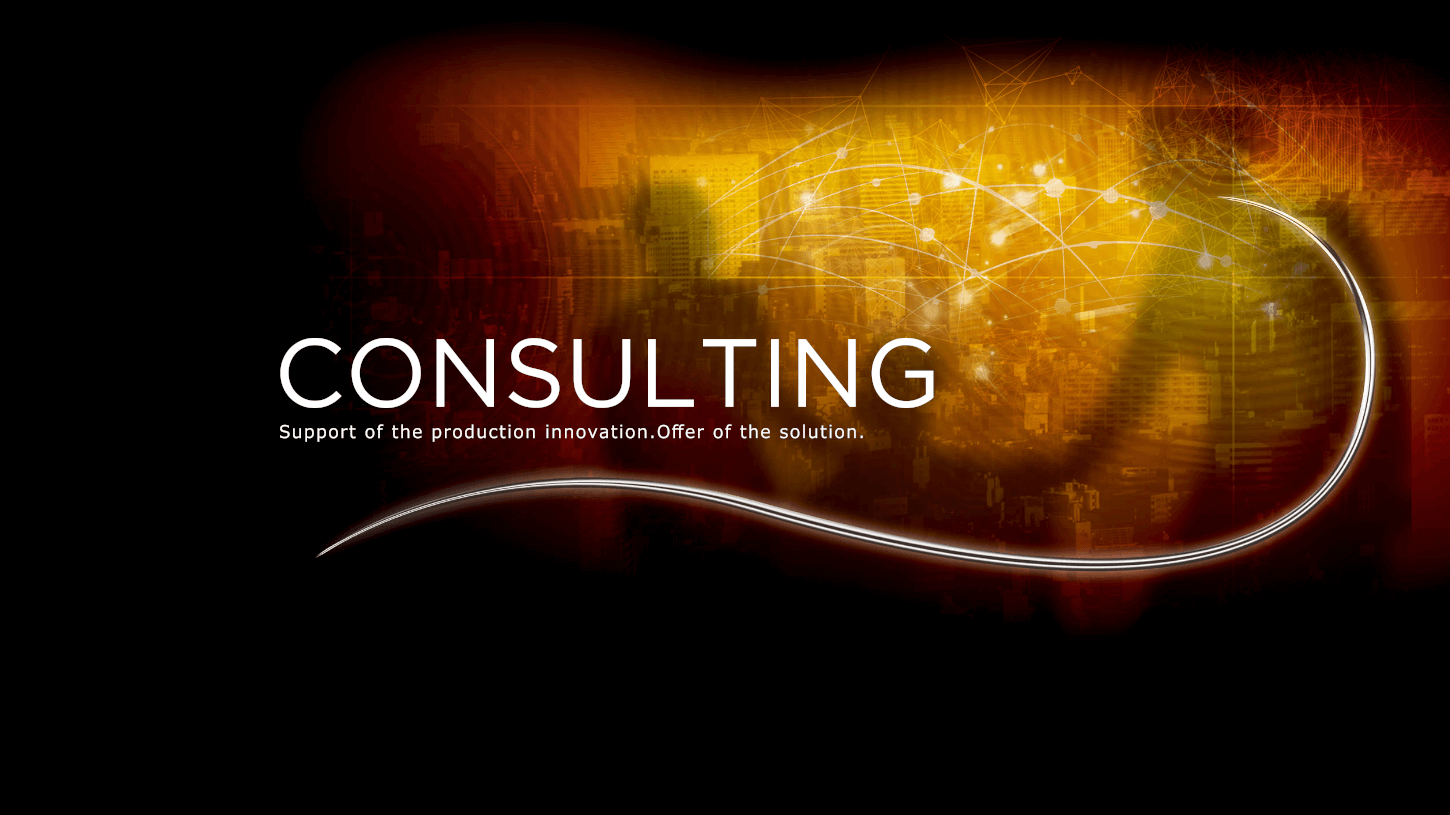
生産革新コンサルティングとは
生産革新コンサルティングとは、レクサー・リサーチがお客様の生産革新、生産システム革新を実現するために掲げられるテーマに対して、ソリューションをご提案するサービスです。
コンサルティングに当たっては、生産システムシミュレータ(GD.findi)を活用いたします。プロフェッショナルコンサルタントの現場経験と GD.findi から出される定量的なデータに基づき、経営、現場の方々に納得いただけるソリューションをご提案いたします。
製造原価目標の設定
製造原価目標設定の重要性と解決の難しさ
多品種生産が進む今日、例えば、多くの派生製品の混在やロングテール製品が生まれる状況が見うけられます。このような場合、原価基準の算定は難しく、製造原価目標が不明確な製品が増えています。製品の生産形態を考える上で、製造原価目標の設定は極めて重要ですが、それらの算定方法や算定基準は現状、お持ちでいらっしゃらないと思います。このようなプランニングの、事業経営における財務への貢献はとても大きいものです。
生産原価目標設定を支援
レクサー・リサーチの生産システムシミュレータであるGD.findiでは、生産を想定する生産工場での当該製品の生産リードタイム、製造に利用する設備等の当該製品の稼働時間割合、工程間在庫量の時間推移を予測することができます。
当該工場での生産ライン、構内物流システム、生産プロセスを設定し、生産計画のデータをGD.findiに与えれば、上記の情報を得ることができます。GD.findiのシミュレーション結果からは、各製品に関わる設備稼働率が分かりますから、設備コストの配布モデル(平均配布コスト、アクティブ・ベース・コスト等)を利用して、製造原価を算出でき、これを製造原価目標として捉えることができます。
生産革新コンサルティングの期間
上記のシミュレーションに利用するデータがすでにお手元にあるのであれば、1ヶ月程度の短期コンサルティングとして対応できます。お客様には、前掲データ、原価配布基準などの原価管理方式をご提供いただくことが前提となります。
多品種少量生産の実現
多品種少量という課題の重要性と解決の難しさ
高度成長時代が終焉を迎えて数十年になろうとしています。しかし、少品種多量生産時代の生産スタイルから抜け出せない工場は未だに多く存在します。これらの工場では、短納期化、多様なユーザニーズ、小ロット化と言ったマーケットからの要求の変化に機敏に対応することが困難です。
このような工場で多品種少量生産に無理矢理対応しようとすると、段取り時間の増加による稼働率低下や滞留時間の増加を引き起こし、従来の高い生産効率を維持することが出来なくなります。
このように多品種少量生産とは、製造業が今日生き延びるためになんとしても解決しなければならない課題でありながら、その課題解決は容易なことではありません。
多品種少量生産実現に向けての支援
多品種少量生産を実現するためのアイデアにはどんなものがあるでしょうか。生産指示という面から考えると、同じ品種を一定の量だけ生産するロット生産に代えて、異なる顧客の注文を注文の速度に合わせて一つずつ流していく、混流一個流しという指示方法があります。また、生産ラインの構成という面からは、製品や部品が工程に向かって流れていくジョブ・ショップ方式、コンベア上を製品が流れていくフロー・ショップ方式、その中間のU字ライン方式、などがあります。これらの選択は、作業者のスキルとも関係し、たとえば、U字ラインに小ロットで注文を流すためには、作業者が多能工のスキルを持っていなければなりません。
個別の機械を見ると、段取り替え時間の短縮が多品種少量生産の必須条件となります。段取り時間を少なくするためには、特別な治具・工具の開発や、外段取り化による実質段取り時間の短縮も必要になります。さまざまなアイデアの最適な組み合わせが多品種少量生産を実現するのですが、アイデアの自由な組み合わせを試行することが、非常に煩雑で膨大な作業になります。
この非常に煩雑で膨大な作業を体系的にスピーディーに実施するために、生産システムシミュレータ(GD.findi)は威力を発揮します。
GD.findiは、工程の編成である、ジョブ・ショップ、フロー・ショップ、U字ラインなどのフロアプランと生産プロセスとを別々に定義できるため、それぞれに複数のケースを想定するだけで、N対Nの試行錯誤を短時間に多量に実行することができます。
また、GD.findiは従来のシミュレータに比べて、その使い勝手は遥かに優れているため、お客様自身でも自由にさまざまなアイデアの組み合わせを仮想的に検証できます。作業の負荷は、従来と比較して圧倒的に軽減され、最適な生産システムを実現できます。
生産革新コンサルティングの期間
お客様の事業規模や課題設定によって期間は異なりますが、簡単な予備調査によって期間と費用をお伝えすることができます。予備調査では、工場、生産ラインを見学し、お客様の事業規模、課題認識、さらに前述しているデータの整備状況等についてインタビューをさせていただきます。通常は1ヶ月~6ヶ月の期間で対応いたします。
本件では、課題設定にもよりますが、経営層、工場マネジメント、生産技術部門、生産管理部門、製造部門、物流部門の方々で構成されるタスクチームが、週1日、最低1ヶ月間は参画していただく必要があります。
自動化機器の投入
自動化機器導入という課題の重要性と解決の難しさ
生産性の向上、品質の安定、また人材不足への対応のための自動組立、自動搬送などの自動化機器の導入は、自動化機器が高価であるため、導入にあたってはその投資効果を十分見極める必要があります。
しかし、その効果を定量的に見定めることは必ずしも容易なことではありません。なぜなら、自動化機器の生産性に対する貢献度は、レイアウト、工程設計、設備編成、作業者編成、段取り装置、生産計画など、複雑に関連する様々な要素に支配されているからです。
生産システムシミュレータ(GD.findi)を利用することで、自動化機器導入に関する判断を正しく行うことができます。加えて、自動化機の導入においては、生産変動に対する柔軟性の維持も課題であり、生産量の変動や生産品目の変更に対する柔軟性を維持する自動化機器導が重要です。生産システムシミュレータ(GD.findi)は、この生産性と柔軟性のトレードオフという問題にもお答えできます。
自動化機器導入検討を支援
生産システム・シミュレーションを活用すると、検証対象の自動化機器の稼働率が把握でき、さらに、工場運営の条件を種々設定することで、稼働率が低下する状況も推察できます。このことから、自動化機器導入に関わる注意点が明確になります。
工場運営の状況を色々と想定した上で、検証対象の自動化機器が一定の稼働率を保っていれば、その自動化が生産性に対して寄与している証明ができたことになります。また、GD.findiで求めた稼働率によって、ABC分析やJ-COSTなど各種の手法により製造原価を算出できるため、自動化前と自動化後の製造原価を比較し、自動化機器導入の効果を財務的見地からも検証することができます。
生産革新コンサルティングの期間
お客様の事業規模や課題設定によって期間は異なりますが、簡単な予備調査によって期間と費用をお伝えすることができます。予備調査では、工場、生産ラインを見学し、お客様の事業規模、課題認識、さらに前述しているデータの整備状況等についてインタビューをさせていただきます。通常は1ヶ月~3ヶ月の期間で対応いたします。
また、お客様がシミュレーションのためのデータを準備できない場合は、レクサー・リサーチのコンサルタントが対象工場でビデオ分析によって収集したり、また、臨時にプログラムを開発して収集したデータに前処理を施したりすることができます。
本件では、自動化機器導入の意思決定に関わるマネジメント層、シミュレーションに必要な各種情報の所在を知る担当者、自動化の具体案や前提条件を検討してきた生産技術、生産管理、物流部門などの方々で構成されるタスクチームを構成し、週1日、最低1ヶ月間は参画していただく必要があります。
工程間在庫の最小化
在庫ミニマム化という課題の重要性と解決の難しさ
工場あるいは物流設備における過剰な在庫は、さまざまな弊害をもたらします。例えば、資金が在庫として固定されることで財務パフォーマンスが低下する、また、在庫が、生産設備や作業者、また管理上の問題を見えにくくするため、改善機会に気づきにくい体質が生まれてしまう、などの問題があります。さらには、在庫によるリードタイムの長期化で、部材状態が変化するなど、品質管理上の問題も生じる原因となります。
在庫ミニマム化を基本とする生産はリーン生産方式と呼ばれ、日本の自動車会社で生まれた生産方式ですが、それは長い間の実践によって蓄えられた各種のノウハウと一貫したシステムに支えられています。そのような実践の歴史を持たない一般の製造業において、生産ラインの混乱を避けながら、在庫の弊害を避けるための取り組みを前に進め、改善意識を磨いていく方法はないのでしょうか。
その手段としては、生産システムシミュレータ(GD.findi)を活用した、仮想ラインによる在庫ミニマム化への取組みがあります。
在庫ミニマム化への取組み支援
在庫を発生させる原因は、工程間能力の差異、安全在庫のような方針、突発的な事故や機械の故障、また生産指示のタイミングのズレなどがあります。生産システムシミュレータ(GD.findi)ではこれらすべてを仮想的に実現あるいは発生させることが出来ます。また、これらの条件を連続的に変化させてシミュレーションを実行することも出来るため、様々な要因の複合的な発生や、限界値・境界値の把握も可能です。
具体的な例として、ある工程間の在庫をミニマム化することが課題であるとします。調査の結果、工程のロットサイズが大きいため、ロットによって使用量にかたよりのある部品は、工程前で長時間滞留し、そのため在庫量が多いことがわかりました。
この場合、在庫量削減のための方策はいくつか考えられます。設備の段取り時間が長く、一定の稼働率を得るためにロットサイズを大きめに設定せざるを得ない場合は、外段取り化や段取り装置の改善などの方策があります。生産スケジュールが取引先に対し、正確に、かつタイムリーに伝えられていない結果、納入タイミングが前倒しになり、それが工程前の在庫量の原因になっている場合もあるでしょう。その場合は、生産スケジュールをタイムリーに通知するITシステムの導入が必要になるかもしれません。これらの方策の妥当性を判断するためには、具体的な設備やITシステムの考案と同時に、あるいはそれに先だって、その効果を生産システムとして判断することが必要なのです。
生産システムシミュレータ(GD.findi)を使えば、段取り装置の改善や導入は、新しいレイアウト、導線情報、工程(プロセス)情報として入力することができ、新旧比較によって、その効果を検証することが出来ます。また、上記のITシステムの導入の効果は、生産・搬送計画の差異として入力し、それも新旧比較によってその効果を検証することが出来ます。段取り装置の改善・導入と、ITシステムの導入のどちらもシミュレーション・モデルに反映させることで、ハード・ソフト両面での改善効果を同時に検証できることは言うまでもありません。
生産革新コンサルティング期間
お客様の事業規模や課題設定によって期間は異なりますが、簡単な予備調査によって期間と費用をお伝えすることができます。予備調査では、工場、生産ラインを見学し、お客様の事業規模、課題認識、さらに前述しているデータの整備状況等についてインタビューをさせていただきます。通常は1ヶ月~3ヶ月の期間で対応いたします。
本件では、在庫ミニマム化のための方策について、導入の意思決定に関わるマネジメント層、シミュレーションに必要な各種情報の所在を知る担当者、在庫ミニマム化のためのハード面、ソフト面での具体案や前提条件を検討してきた生産技術、生産管理、物流部門、情報システム部門などの方々で構成されるタスクチームが、週1日、最低1ヶ月間は参画していただく必要があります。