シミュレーション統合生産 SIM
Simulation Integrated Manufacturing
IoT 時代のサイバーフィジカル生産コンセプト「シミュレーション統合生産(SIM)」
SIMはIoT時代のモノづくりへと革新するコンセプトです。 IoTと超並列シミュレーション等を駆使したAI(人工知能)技術により生産活動の最適化を行い、IoT時代のサイバーフィジカル生産を推進します。
「シミュレーション統合生産」を進める背景と目的
グローバル化や多品種少量生産の時代を迎えた今日、カイゼンやすり合わせ活動では国際競争力を得ることが困難となってきました。変化し、変動する時代における新しいものづくりの在り方へ移行することが求められています。
一方、IoTの進展の中、ドイツではインダストリー4.0による「水平分業」、米国ではGEを中心とした「高付加価サービス化」等、各地域の産業文化を踏まえた生産革新を進めようとしています。それに対し、日本はロボット技術などの要素技術の対応に留まり、本質的なコンセプトを創り上げる活動には至っていません。ドイツ、アメリカ、日本の産業文化や強みは全く異なります。
重要なことは、自動化技術などでインダストリー4.0などの後追いすることではなく、日本のもつ本質的な強みをイノベーションすることです。つまり、日本は、そもそもオペレーション力で「垂直連携」強みを発揮してきたわけで、この強みを最新の技術でイノベーションし、『予測的エンジニアリング』を実現し、事前に問題を察知して対策しておく能力や、変化や変動へ対応する能力を獲得することが有効です。
尚、「予測的エンジニアリング」とは、上流エンジニアリング業務で生産システムを計画する段階で徹底的に問題を抽出して対策する技術です。事後のカイゼンを行うことなく、計画段階で最高の性能や品質を導出します。ICT、IoTと日本のものづくり力が結合する次世代のものづくりを目指します。
「シミュレーション統合生産」の具体的な取り組み
このような背景の中、当社では「予測的エンジニアリング」により、エンジニアリング業務の組織能力を強化する「シミュレーション統合生産(Simulation Integrated Manufacturing)」と呼ぶ新しいコンセプトを進めています。
生産シミュレーションを活用して上流業務を連携させるとともに生産現場をIoT化して生産マネジメントを革新し、さらには従来の分散型の業務運用から集約型の業務運用へと転換して、エンジニアリング業務をイノベーションします。そのアプローチとしては、量産に至るまでの上流業務と、量産開始以降の下流業務に分けて、以下の2つのテーマを推進しています。
【1】生産エンジニアリング業務の垂直統合の実現
【2】動的最適化型生産システムの実現
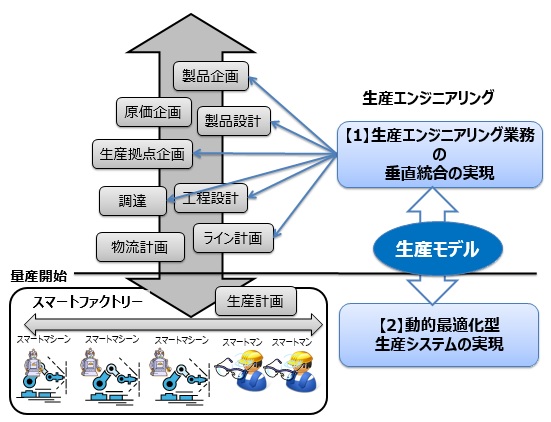
各テーマの具体的な内容を以下に詳細します。
【1】生産エンジニアリング業務の垂直統合の実現
ものづくりの上流業務は、製品企画や原価企画、拠点戦略などの企画から始まり、設計、調達、工程設計、ライン計画などを経て生産体制を作り上げて量産に至ります。ここで、これらの業務において、「生産システム」の概念ベースに置くと、それぞれの業務が「生産モデル」を通じて有機的に連携させることができます。さらに生産シミュレーションを活用し、製品や部品、生産設備、レイアウト、治工具などの「モノ」と、作業や工程、搬送、物流、生産計画などの「コト」を意味的に結合することで、その関係の合理性や成立性を検証することができます。
生産エンジニアリング業務の垂直統合のために各種のプランニングサービスを構築し、各業務プロセスにおいて生産シミュレーションで評価しながら、その成立性や効率性を検証して業務を進めることで、上流業務の効率化と組織能力の最大化を図ります。
これは、従来の部分最適からビジネスプロセス統合型の全体最適へと転換するためのエンジニアリング技術の実現を意味します。また、IoTを最大限に活用して生産現場の実体と同期することができる「グローバル・ファクトリ・レポジトリ」と呼ぶ工場データベースを実現し、生産エンジニアリング業務のためのプランニングに活用します。
【生産エンジニアリング業務の垂直統合】
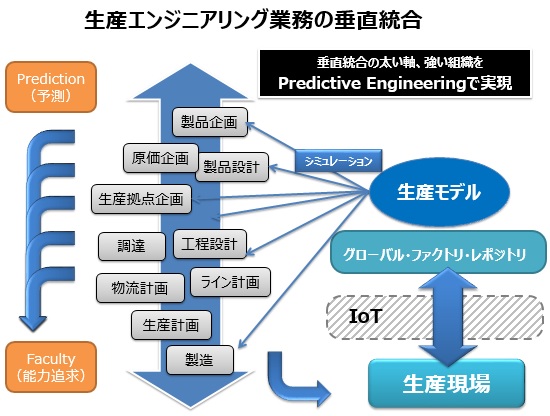
この内容について従来方式と比較して、その狙いを説明します。
A)従来、各組織に渡る業務プロセスマネジメントはあいまいであり、結果、修正手戻りが多く発生したが、予測的エンジニアリング技術により事前対策を進めることで、手戻りを撲滅すること
B)従来、ERP、PLMなどのデータ共有方式による確定的、かつ、抽象度の高いモデル構造では、量産までのすべてのエンジニアリング業務を適切な精度や粒度でカバーできなかったが、マルチスケール化と循環型運用のための管理機構により生産モデルの利用に柔軟性を与えることで、広い範囲の業務をカバーすること
C)従来、モデルの抽象度が高く、物理的情報が乏しいために生産現場との「かい離」があったが、実体を精度高く表す生産モデルとIoTを活用して現場に同期することで、生産現場に則した計画を立案できるようにすること
D)従来、エキスパートの知見は属人化され、現場での個別活動に閉じるしかなかったが、エキスパートの持つ実効性のある経験知を生産モデルとして展開し、他者が参照、再利用することで、個の知から組織の知へと昇華させること
これらに対応するためには単にモデル化や機能化を進めることだけではなく、さらに踏み込んで「生産現場そのもの」を表す生産モデルを追求するとともに、エキスパートの知見を反映したそれらの意味的な結合を実現するメソッド化を徹底的に追及しながらシステムへ知見を集積し、これを軸としてエンジニアリング業務を進めることが基本的なアプローチです。
【2】動的最適化型生産システムの実現
量産に入ったのちには、生産現場ではマシントラブルや不具合対応、特急品対応のようなトラブルが起こることは日常茶飯事で、如何にそのトラブルを乗り越えて、本来の生産に戻る力が求めらます。これを「復元力(レジリエンス)」と言うが、生産現場では一般的に対応が難しく、実際、予定された生産計画が崩れ出したらなかなか、元に戻りません。
動的最適化型生産では、設備のチョコ停やドカ停、特急品への対応、また、調達部品の未達、品質問題の発生などのトラブルが起きたときに、リアルタイム生産シミュレーションを活用して問題の影響や波及を予測します。そして、そこに問題があるならば、超並列シミュレーションによる最適化技術を駆使し、生産計画や生産ラインの割り当て、要員計画をはじめとする様々な生産リソースをその場で逐次、変更しながら、本来の状態に戻すべく、もしくは問題を回避するべく、自律的に調整を図る。つまり、生産シミュレーションを活用して、生産における変動や障害、外乱に対応する能力を獲得することが基本的なアプローチです。
実際の運用にはIoT技術を活用します。人間系が関わる生産ラインではサイバー・フィジカル・システムを活用して作業指示と作業実績のモニタリングを行いながら生産を実行します。また、設備系が中心の生産ラインではMES、また、スマートマシンを活用して作業実績を獲得しながら生産を実行します。そして作業の遅延が発見されたとき、また、断続的に超並列シミュレーションによる動的最適化を行い、生産計画や生産体制を逐次、修正し続け、適切な生産状態を維持します。
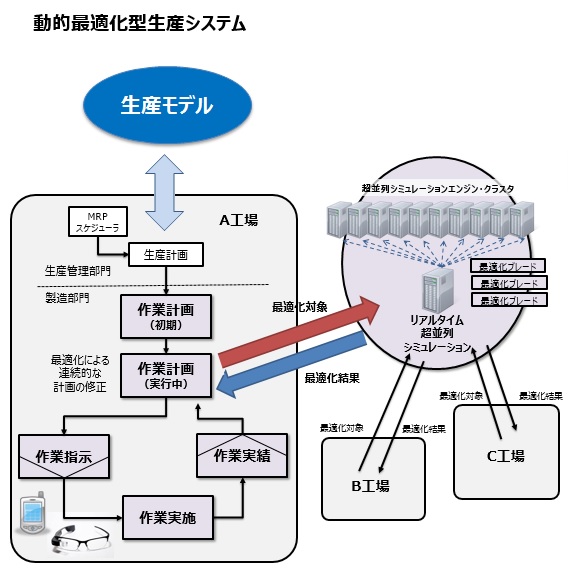
SIMの位置づけを以下に示します。SIMはPLM、ERPやMESとは相互補完関係にあります。従来、PLM、ERP、MES等のシステムはその体系の中で閉じていたが、それらを連携させて統合的なエンジニアリングを進める環境を提供することがSIMの狙いであるとも言えます。生産モデルをそれらのシステムの中核に据えることで、有機的な連携を図りたいと考えています。
【「シミュレーション統合生産」の位置づけ】
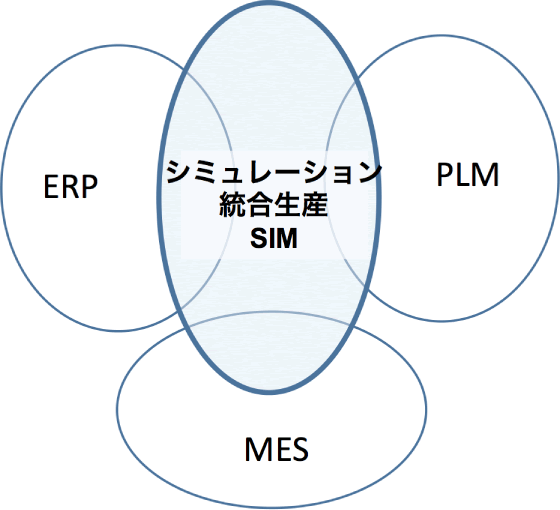
「シミュレーション統合生産」をご紹介するセミナをご参考にしてください。
生産システムシミュレータ GD.findi は下記をご覧ください。