第14回:生産計画を決めよう! ~設備の段取りロスを考慮した生産計画の策定~
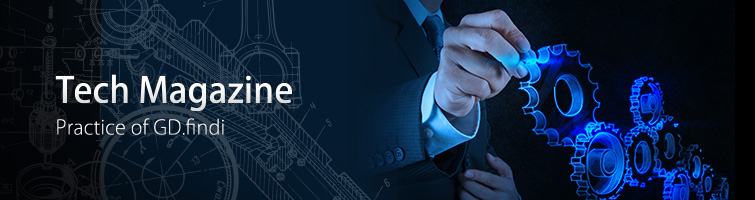
小ロットで多品種の生産が求められている今、製品切替時の設備段取りによるロスの問題は、以前の Tech Magazine でもご紹介いたしました。
段取りによるロスを削減するための方法の 1 つとして「部品の流し方」すなわち設備が担当する加工プロセスの割当をそれぞれ設定することをご紹介いたしましたが、実際は設備の割当を限定することができないケースもあります。
今回は設備の割当を限定せず、生産計画を決める中で、段取りロスを極力減らすような計画を作成する場合を考えます。
1.モデルの作成
まずは前回(第13回:作業の条件を決めよう!)でご紹介したモデルに、複数の製品を生産する工程を作成します。
もう 1 つの製品の生産プロセスとして、以下の行程を考えます。
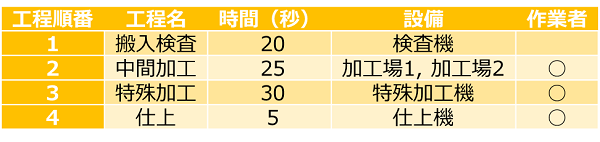
ここで、 [作業者] が “○” となっている工程は、その工程を行う作業者が誰か 1 人必要であることを指します。
これを GD.findi で表現すると以下のようになります。

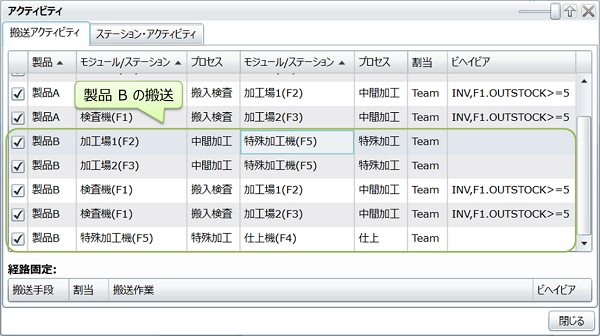
また、製品Aから製品Bへの切り替えにおける段取り、製品Bから製品Aへの切り替えにおける段取りの設定は以下のようになります。
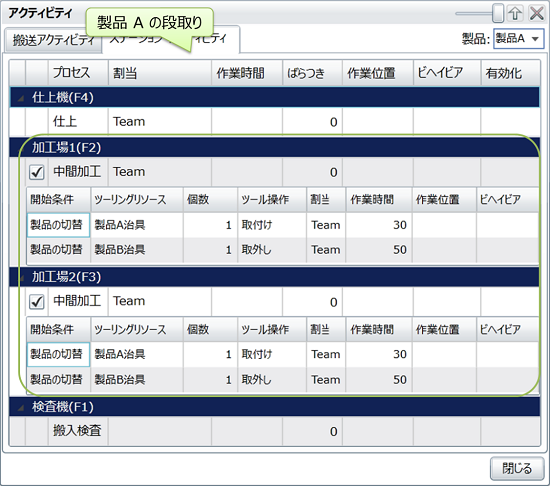
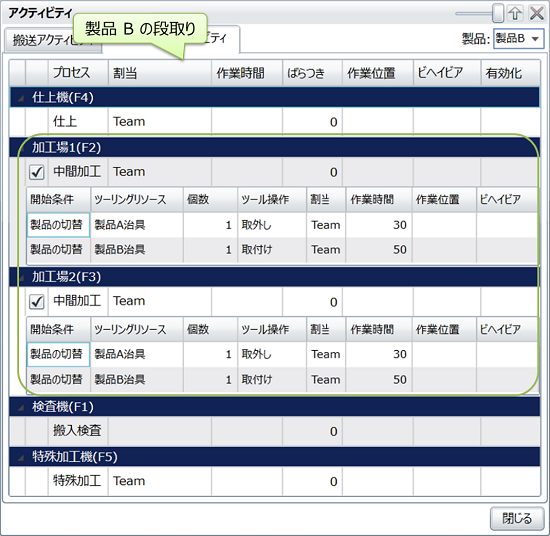
さらに、製品Bのステーション・アクティビティでの割当には “Team” を設定します。
2.生産計画の設定
この生産モデルで生産する製品の投入計画を、まずは以下のように設定してみます。
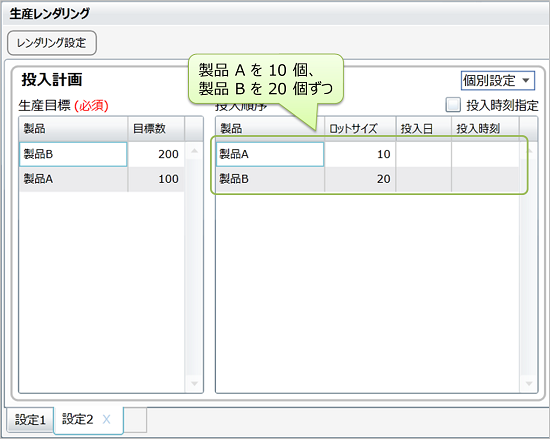
この設定で、シミュレーション結果をみてみましょう。
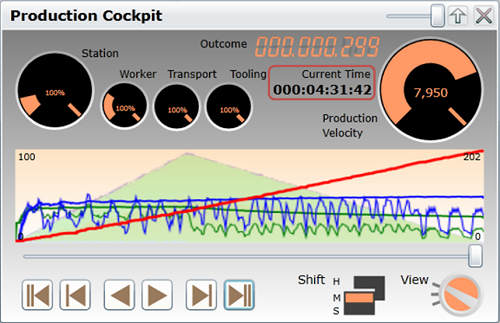
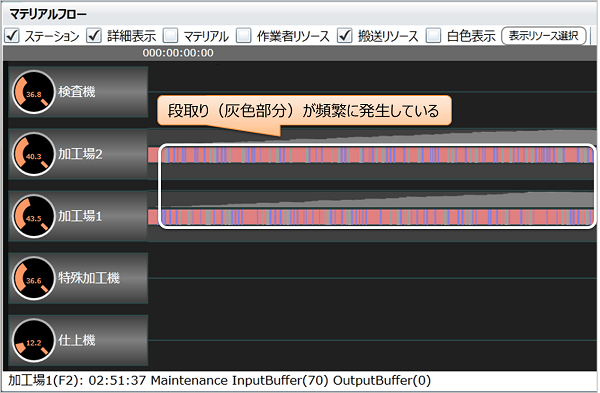
マテリアルフローを見ると、加工場1 および加工場2 における段取りが頻繁に発生していることが分かります。
3.生産計画の変更
一般に、生産ロットを大きくすれば、段取り回数が減り、生産能力が上がると考えられています。
そのロットサイズは製品の納期や納入の計画を考慮して策定されますが、ここでは投入計画で投入する個数を大きくして、シミュレーション結果を見てみます。
たとえば、投入計画の個数を製品 A は 5 個ずつから 10 個ずつ、製品 B は 10 個ずつから 20 個ずつ投入するように設定してみましょう。
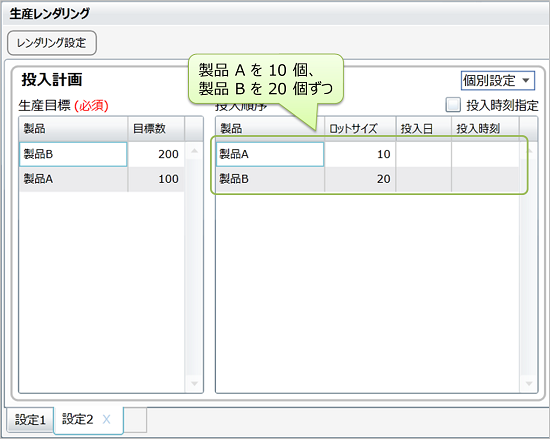
結果は以下のようになりました。
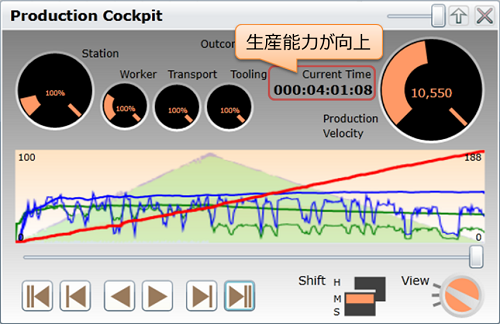
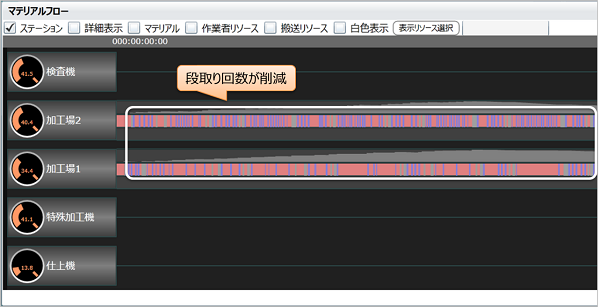
シミュレーション結果からも分かる通り、ロットサイズを大きくすることで、段取りの発生回数を減らすことができ、そのロスが減った分、生産能力が向上していることが分かります。
前述のとおり、生産計画は様々な要因を考慮して策定することが一般的ですが、その要因の 1 つである「複数製品生産時における段取りによるロス」を、 GD.findi を活用して測ることが可能です。
他の制約も考慮した状態で、適切なロットのサイズを決める際に、同様のシミュレーションを行うことで、結果を見比べながらプランを立てることが可能です。
なお、GD.findi に関する詳細は下記ページよりご覧ください。